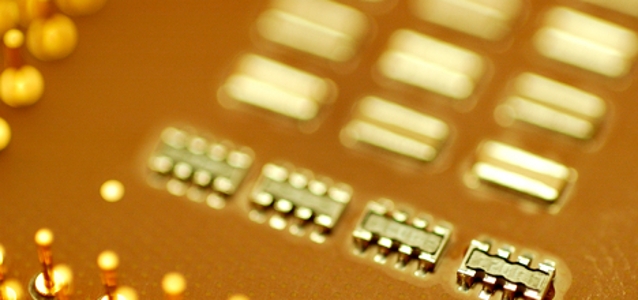
© Grzegorz Wolczyk / Dreamstime
Analizy |
Co tak naprawdę siedzi w AOI ? cz.1.
Autorzy tekstu przedstawiają zasadnicze różnice w pracy dwóch podstawowych typów AOI: automatów opartych na porównywaniu obrazu oraz opartych o algorytm.
Wprowadzenie
Rozpatrując odpowiednie metody inspekcji, mające spełnić wymagania produktywności i jakości procesów technologicznych, obecnie większość inżynierów zwraca się ku rozwiązaniom opartym na automatach. Jako że liczba producentów AOI wzrosła w ostatnim czasie, inżynierowie mają do dyspozycji cały szereg rozwiązań, co czyni proces wyboru odpowiedniego rozwiązania coraz trudniejszym.
Celem artykułu jest pomoc potencjalnym użytkownikom AOI w wyborze i lepszym zrozumieniu różnic pomiędzy poszczególnymi konstrukcjami. Artykuł przedstawia zasadnicze technologie oraz koszty, związane z zakupem, obsługą i użytkowaniem sprzętu.
Pierwsza część artykułu, nazwana ‘Podstawy AOI’, bliżej przedstawia dwie odmienne, dominujące na rynku rozwiązania technologiczne: AOI oparte na analizie obrazu (Image Based AOI) oraz AOI oparte na analizie algorytmu (Algorithm Based AOI). Każda z tych technologii oferuje odmienne walory w procesie inspekcji.
© Vi TECHNOLOGY
Niektóre systemy AOI dysponują paletą barw i odpowiednimi źródłami światła, celem zapewnienia możliwie najlepszej pracy z wszystkimi rodzajami materiałów, mającymi zastosowanie w procesie montażu PCB. [1].
Kierunek rozchodzenia się światła oraz jego źródła są czynnikami, których uwzględnienie jest konieczne w procesie porównywania AOI. Różne źródła światła są jednym ze sposobów na polepszenie kontrastu, a co za tym idzie, poprawę jakości i stabilności obrazu. Podobnie, różnicę stanowi również to, czy światło jest ukierunkowane czy rozproszone. Obecnie, większość systemów używa światła padającego osiowo lub pod określonym kątem. Jest to kluczowy element inspekcji połączeń lutowniczych, w szczególności w połączeniu z kolorem światła. Najbardziej zaawansowane maszyny AOI używają światła kierunkowego, prostopadłego oraz umieszczonego pod kątem, dodatkowo w 3 różnych kolorach. Ilustracje poniżej obrazują różnice uzyskanego kontrastu przy zastosowaniu światła prostopadłego oraz ustawionego pod kątem.
Każdy proces automatycznej inspekcji zaczyna się od cyfrowej akwizycji obrazu, uzyskiwanego przy wykorzystaniu kamery, oświetlenia i soczewek. Tak uzyskany obraz prezentuje coś, co możemy określić jako scenę: obiekty, kształty, tło. Obraz to z kolei nic innego jak tylko macierz, złożona z pikseli, gdzie piksel jest określany jako najmniejsza jednostka obrazu. Macierz zawiera więc następujące informacje o każdym z pikseli: lokalizację wg kolumn i rzędów oraz intensywność światła, mierzoną albo w skali szarości (Black & White, B&W), albo wyrażoną przez wartość RGB (Red, Green, Blue) dla obrazów kolorowych. Podczas porównywania rozwiązań AOI, jakość obrazu określa się zwykle poprzez rozmiar piksela, wyrażony najczęściej w mikronach. Rozmiar piksela oblicza się poprzez podzielenie pola widzenia (Field of View, FOV), czyli rozmiarów kontrolowanego obszaru, przez parametry matrycy CCD lub CMOS. Przykładowo, jeśli w AOI zastosowano kamerę 4M (4 miliony pikseli, 2000 x 2000), a pole widzenia FOV wynosi 38mm x 38mm, rozmiary piksela wynoszą 19 mikronów. Jednak, określając jakość obrazu jedynie poprzez rozmiar piksela, łatwo jest nie docenić znaczenia oświetlenia i soczewek. System oświetlenia może być opisany poprzez długość fali, jak również kierunek rozchodzenia się światła (rozproszone, góra-dół, ustawione pod kątem) i jego jednorodność. Wystawiając badany obiekt na światło różnego koloru, można otrzymać różne obrazy. Obiekt, w zależności od jego zdolności pochłaniania czy odbijania światła, reaguje odmiennie w zależności od długości fali świetlnej (grafika poniżej). Kluczem jest uzyskanie kontrastu pomiędzy badanym obiektem a jego tłem, którym zwykle jest płytka PCB.© Vi TECHNOLOGY

Obraz z pola widzenia maszyny AOI zawiera cały szereg komponentów, posadowionych na płytce PCB. Niektóre z tych komponentów są identyczne i jako takie powinny być rozpoznane przez AOI. Niestety, w rzeczywistości, identyfikacja przez AOI nawet identycznych elementów może wskazywać, iż są to komponenty różne [wg wskazań systemu]: dzieje się tak ze względu na problemy związane z jednorodnością światła w polu widzenia lub problemem paralaksy, występującym przy nie-telecentrycznych soczewkach. Każdy z tych problemów może być przyczyną fałszywych alarmów.© Vi TECHNOLOGY
W praktyce, jeśli pozyskany obraz pola widzenia zawiera pewne optyczne odkształcenia (na przykład jeśli komponent znajduje się na jego skraju) lub jeśli światło jest jaśniejsze w centrum pola widzenia, identyczne komponenty w różnych lokalizacjach będą wydawały się różne. Pewnym rozwiązaniem tego ograniczenia jest zastosowanie przez programistę AOI pewnych tolerancji i akceptacja pewnego stopnia wariancji obrazu, co jednak równocześnie stanowi kompromis w zakresie rzetelności testu. Uzyskanie obrazu o jednorodnym świetle, wolnym od efektu paralaksy oraz o odpowiednim kontraście odbywa się kosztem szybkości pracy lub rozdzielczości pola widzenia, względnie rozmiaru piksela. W przypadku większości producentów AOI, zależność ta da się opisać prostym równaniem: przy zmniejszeniu rozmiaru piksela o czynnik ‘n’, czas pracy wzrasta o (1/n)2 (przy założeniu zastosowania tej samej kamery). Mając na uwadze powyższą zależność, potrzeba inspekcji coraz to mniejszych komponentów wpływa na jakość kontroli lub długość cyklu pracy. Niektórzy producenci AOI odpowiedzieli oferując całą gamę kamer lub głowic (kamera + soczewka + oświetlenie), dostosowanych do inspekcji zarówno małych, jak i dużych komponentów. Jednak, maszyna wyposażona nawet w różne kamery, wciąż musi rozwiązać problem dokładności i czasu pracy. Istnieją jednak rozwiązania, eliminujące konieczność kompromisu pomiędzy cyklem pracy a jakością inspekcji. Jedną z nich jest technologia ‘sub-pixel’. Opracowana przeszło dekadę temu, rozdzielczość sub-pixelowa może być uzyskana w obrazach cyfrowych, zawierających dobrze zdefiniowane linie, punkty czy krawędzie, których pozycja na obrazie może być dokładnie zmierzona za pomocą odpowiedniego algorytmu. Tego typu algorytm odczytuje dane z obrazu z dokładnością przekraczającą nominalną rozdzielczość, wyrażoną w pikselach. Kategorie AOI Co prawda kamera, optyka oraz oświetlenie odgrywają kluczową rolę w każdej maszynie AOI, lecz prawdziwą różnicę pomiędzy nimi stanowi oprogramowanie, zastosowane do obróbki obrazu. Unikając opisu niekończącej się listy szczegółowych rozwiązań, dostępnych obecnie na rynku, wszystkie AOI można przypisać do jednej z dwóch zasadniczych kategorii: AOI oparte na analizie obrazu oraz AOI oparte na analizie algorytmu. AOI oparte na analizie obrazu AOI oparte na analizie obrazu (nazywane też AOI opartym na porównywaniu obrazu), jako podstawową informację wykorzystują siatkę pikseli, zawartą w uzyskanym obrazie. Wczesne systemy używały rozwiązań opartych na odcieniach szarości, porównując każdy piksel w badanym rejonie obrazu.© Vi TECHNOLOGY
Na obrazach zamieszczonych obok widać ten sam komponent, jednak na jednym z nich jest on umieszczony pod innym kątem. Stosując metodę porównywania każdego piksela w skali szarości, drugi z obrazów powinien nie przejść testu ze względu na brak informacji o obecności niektórych pikseli w badanym rejonie płytki. Obrazuje to bardzo słabą dokładność tej metodologii w przypadku przekrzywionych komponentów. Postęp w technikach obróbki obrazu, wraz z postępem w dziedzinie technik obliczeniowych, pozwolił na znaczne udoskonalenie technologii opartych na porównywaniu obrazu. Większość systemów opiera się obecnie na odpowiednich zasobach, bibliotece obrazów. Pozwala to na przejrzenie obrazów zidentyfikowanych komponentów, dobrych oraz wadliwych, celem inspekcji płytki i odnalezienia tych wadliwych. Wyniki testu zależą więc od jakości dostępnej biblioteki obrazów, tworzonej na podstawie zmontowanej wcześniej płytki lub płytek.© Vi TECHNOLOGY
Technologie oparte na analizie obrazu kwalifikują komponent w na podstawie porównania uchwyconego obrazu komponentu z jego obrazem z biblioteki poprawnych i wadliwych komponentów. Różnorodność samych technik porównywania rozciąga się od technik bazowych do sieci neuronowych, jednak kluczowe pytanie, zadawane przez AOI opartego na analizie obrazu zawsze jest takie samo: ‘Czy mój obecny obraz wygląda tak samo jak obraz składowany w moim banku zdjęć?’ Po przeprowadzeniu porównania, AOI da jedną z dwóch odpowiedzi: ‘Tak, to dobry komponent’ albo ‘Nie, musze go jeszcze porównać z kolejnym zdjęciem z biblioteki’. Proces porównywania trwa aż do momentu, kiedy komponent ostatecznie jest uznany za wadliwy lub kiedy zostanie odnalezione zdjęcie, wskazujące, że komponent może być pozytywnie zaklasyfikowany. Ze względu na różnorodność przeprowadzanych procesów, systemy oparte na porównywaniu obrazu muszą stosować olbrzymie i stale rosnące biblioteki obrazów, co ma ujemny wpływ na czas pracy. Niektóre systemy analizy obrazu próbują kompensować ów ujemny wpływ poprzez tworzenia modeli, obrazujących różnorodność przeprowadzanych procesów za pomocą podejścia statystycznego, w połączeniu z szybką akwizycją obrazu. W opisywanej metodzie, rozbudowany bank obrazów jest upraszczany poprzez kalkulację średniej i standardowej dewiacji dla każdego piksela, wyrażonej w skali szarości. W tak określonym modelu inspekcji, ‘odległość’ [stopień odmienności] pomiędzy modelowym oraz rzeczywistym komponentem jest podstawą do sformułowania werdyktu – dobry lub zły. Jako że AOI zbiera obrazy wielu komponentów i dodaje je do bazy, ‘statystyczny’ obraz staje się słabo zdefiniowany, a samo AOI traci swoją zdolność do oddzielenia dobrych i złych komponentów. AOI oparte na algorytmie Dzięki osiągnięciom matematyki i geometrii, AOI oparte na algorytmie, aby odnaleźć komponent na uchwyconym obrazie płytki, stosuje techniki rozpoznawania obrazu. Zamiast więc porównywania jednego obrazu z drugim, technologia ta odnajduje zdefiniowane wzory (opis geometrii lub schemat obiektu) na obrazie.© Vi TECHNOLOGY
Technologia ta daje duże możliwości, ponieważ komponent jest zdefiniowany wyłącznie przez swój kształt, bez względu na skalę szarości czy informację o poszczególnych pikselach. Technologia oparta na algorytmie oferuje lepsze możliwości również ze względu fakt, iż nie zachodzi potrzeba porównywania poszczególnych pikseli i w konsekwencji zmiany w otoczeniu nie mają ujemnego efektu na wynik testu. Nieznaczne zmiany koloru komponentu czy płytki nie wpływają na zdolność AOI opartego na algorytmie do dokładnej identyfikacji komponentu. Kolejne ilustracje opisują, w jaki sposób technologia odnajdywania wzoru stosowana jest do odnajdywania obiektu w zmiennym otoczeniu oraz przy różnym oświetleniu. W przypadku AOI, technologia odnajdywania wzoru znajduje zastosowanie do zdefiniowania kształtu [wzoru], opisującego konkretny komponent. Dla przykładu, poniższe wzory mogą służyć do zdefiniowania kondensatora 0201 czy 01005. Definicja może być stworzona poprzez zastosowanie ‘obrazu syntetycznego’ (a) lub po prostu poprzez zdefiniowanie kształtu komponentu (b). Kiedy już definicja zostanie zachowana w oprogramowaniu, system inspekcji analizuje zebrane obrazy poszukując na nich odpowiedniego wzoru w lokalizacji opisanej przez indeks lokalizacji komponentu oraz wartości X, Y i teta. Można stosować kilka technik odnajdywania wzoru, jednak najdokładniejsza jest technika nazywana obrazowaniem wektorowym (Vectoral Imaging).© Vi TECHNOLOGY
Jak pokazano na rysunku obok, system odnajduje krawędzie komponentu, określając je za pomocą serii wektorów (zielone linie na obrazku). Używając interpolacji matematycznej oraz techniki rozdzielczości sub-pikselowej, wektory lepiej opisują faktyczny kształt komponentu niż siatka pikseli. Zapewnia to znacznie lepszą dokładność w procesie porównywania faktycznego komponentu z jego obrazem, zawartym w bibliotece komponentów. Przy inspekcji połączeń lutowniczych, wyniesień czy mostków, dokładna lokalizacja komponentu jest czynnikiem krytycznym i takich przypadkach wymagana jest najwyższa dokładność. Klucz do zrozumienia różnicy Jak zobrazować różnicę pomiędzy AOI opartym na analizie obrazu i opartym na algorytmie w jednostce, która byłaby ważną miarą przy produkcji elektronicznej? Zakładając, iż nadrzędnym celem AOI jest redukcja błędów na PCB, system musi efektywnie wykrywać wszystkie wadliwe komponenty, możliwe do wykrycia w danym etapie produkcji. Jednak doświadczenie pokazuje, iż w pewnych warunkach, AOI przepuszczają błędy. Przepuszczone błędy mierzone są miarą nazywaną false accept rate (FAR), wyrażoną w ppm (komponenty na milion, parts per million) i obliczaną jako stosunek ilości przepuszczonych wadliwych komponentów oraz liczby sprawdzonych komponentów ogółem. Bardzo często poza FAR, obliczana jest również miara FCR (false calls rate), mierząca w ppm ilość dobrych komponentów rozpoznanych przez maszynę jako wadliwe. FCR ma bezpośredni wpływ na płynność oraz jakość procesu. Jeśli ilość fałszywych alarmów jest zbyt wysoka, rośnie również prawdopodobieństwo przepuszczenia rzeczywistych defektów. Widzieliście kiedyś operatora, akceptującego fałszywe alarmy i jednocześnie przepuszczającego błędy? Przy wysokim wskaźniku fałszywych alarmów, operator jest nimi zmęczony i w rezultacie skłonny przepuszczać faktyczne błędy. Faktyczne błędy stają się wówczas ‘fałszywymi akceptami’, bowiem operator w niedostatecznym stopniu skupia się tropieniu faktycznych defektów. Również czas pracy inspekcji jest kluczowym czynnikiem w procesie SMT, a AOI dokonujące 100-procentowej inspekcji nie powinno stać się wąskim gardłem całego procesu. Zdarzały się przypadki, kiedy deaktywowano pewne funkcje testowe AOI, aby tylko osiągnąć odpowiedni czas pracy maszyny. Większość nabywców AOI, jako kluczowy czynnik w procesie wyboru maszyny bierze pod uwagę również czas programowania. Czas programowania zawiera takie czynniki jak transfer danych z CAD do programu operacyjnego AOI oraz ich precyzyjna obróbka, celem ich dopasowania do zróżnicowanych warunków procesu produkcyjnego. Kolejnymi dwoma czynnikami są wartości Program Portability (PP) oraz Process Control (PC). Pierwszy z nich, PP, ma kluczowe znaczenie dla tych użytkowników, którzy będą dokonywać częstych zmian linii, obsługiwanych przez AOI. Przykładowo, kiedy zajdzie potrzeba przeniesienia produkcji z linii 1 na linię 2, stosowanie tego samego programu, bez konieczności wprowadzania czasochłonnych modyfikacji, jest niezwykle ważnym kryterium. Drugi z czynników, PC, jest ważny dla tych użytkowników, którzy nie tylko chcą wychwycić defekt, ale również udoskonalić proces produkcyjny poprzez odnalezienie jego przyczyny i korektę. Takie cechy AOI jak dokładność i powtarzalność są więc kluczowe dla obu omawianych czynników. Dokończenie artykułu w za tydzień, 20 lipca. Bibliografia [1] Vi TECHNOLOGY i-LITE construction, Romain Ramel, 2007 [2] Performance Comparison of 2D object recognition Techniques, Markus Ulrich, Carsten Steger, ISPRS 2002 [3] Vectoral Imaging: a new direction in Automated Optical Inspection, Mark Norris, 2002 Autorzy Marc Brun, Marketing Manager, Vi TECHNOLOGY Russell Claybrook, Western Regional Sales Manager of Vi TECHNOLOGY Jean-Marc Peallat is the President and CEO of Vi TECHNOLOGY Russ Warnecke is the Applications and Support Manager of Vi TECHNOLOGY© Vi TECHNOLOGY