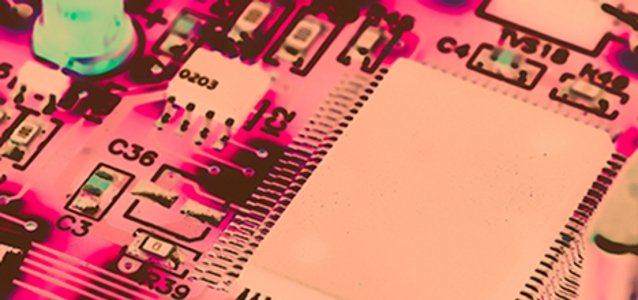
© Anthony Bolan / Dreamstime
Analizy |
Poprawa procesu drukowania pasty
Poprawa procesu drukowania pasty poprzez fazowe przesunięcie interferencyjne - nowa technologia pomiarowa pozwala na wysoki stopień weryfikacji błędów.
Już od dawna wiadomym jest, że w procesie lutowania SMT pasta została uznana za główne źródło wad montażowych. Sam proces jest enigmatyczny – jest to połączenie sztuki i nauki i zdecydowanie nie można nazwać go prostym.
Podczas ewaluacji technologii montażu powierzchniowego próbowano wymyślić przeróżne narzędzia, które miały służyć do kontroli pasty. Urządzenia te bazowały na najnowszych osiągnięciach w dziedzinie optyki, wykorzystywały lasery i skomplikowane systemy wizyjne. Niestety podczas dążenia do ciągłej miniaturyzacji elementów czegoś zabrakło stosowanym urządzeniom – dokładności, czasu taktu lub obu naraz. Możliwość rozpoznawania depozytów 0,010° na tyle dobrze, aby powierzyć jakość naszej produkcji i na tyle szybko, aby spełnić wymagania i nie opóźnić produkcji stał się Świętym Grallem automatycznej inspekcji pasty.
Jak to działa?
To właśnie wtedy badania nad interferometrią i przesunięciami fazowymi zaowocowały stworzeniem nowej technologii kontroli pasty i zmienił sposób jej postrzegania. Jak to działa? Prosta zasada fizyki – wyobraź sobie słońce świecące przez żaluzje. Promienie słoneczne tworzą wzór pasów, na przemian jasne i ciemne. Te paski pojawiają się prosto na płaskich powierzchniach, takich jak podłogi, stoły, ale wydają się odbiegać gdy krzyżują się z meblami i zmieniają sposób ich postrzegania – zostają przesunięte tworząc płaską topografię.
Rysunek 1. Wzór MoiréIlość postrzeganych zygzaków zależy od wysokości obiektu oraz względnie od kąta obserwacji i źródła światła. Podejmując kilka pomiarów w znanych odstępach czasu, wysokość z powierzchni można obliczyć matematycznie. Na przemian jasne i ciemne paski są znane jako wzór Moiré (Rysunek 1), a metoda pomiaru w znanych odstępach czasu nazywana jest interferencyjnym przesunięciem fazowym (Rysunek 2) System inspekcji firmy Koh Young wykorzystuje opatentowaną metodę zastosowania przesunięcia interferencyjnego do pomiaru depozytów pasty lutowniczej. System dzieli każdy depozyt na malutkie części jak np. 10μm i mierzy lokalizację oraz wysokość każdego segmentu (Rys. 3). Następnie system oblicza objętość poszczególnych segmentów i tworzy model 3-D całego depozytu pasty (Rys. 4). Model pomiaru objętości, wysokości i lokalizacji obszaru zostaje zapisany i porównany z idealnym przykładem. Modelowanie jest niezwykle dokładne i wykazuje powtarzalność i odtwarzalność z różnicami nie mniejszymi niż 10%. Przykładem może być firma Victor Corporation, producent komponentów dla elektrowni, obecne używający sprzętu Koh Young w celu kontroli prototypów i linii produkcyjnych.© PB Technik Rysunek 2. Diagram przesunięcia interferencyjnego
© PB Technik
Rys. 3 Elementy depozytu pasty lutowniczej mierzone za pomocą przesunięcia fazowego.Produkowane przez nich pakiety zawierają jedne z najmniejszych i najbardziej złożonych pakietów SMT: elementy ułożone na obszarze 0,5 mm, elementy QFN i SOT 883s oraz pasywne 0201. Płytki są produkowane w panelach od 10 do 20 rzędów, względna ilość depozytów pasty przekracza 10 000, większość z nich jest mniejsza niż 0.012`` - oczywiście taki proces nie jest niemożliwy, ale z pewnością stanowi nie lada wyzwanie. Ray Whittier, starszy inżynier procesu jest odpowiedzialny za przeprowadzenie kontroli. Używa do tego technologii przesunięcia fazowego zarówno online jak i offline. Zarządzanie procesem online obejmuje wydruki badań przesiewowych pod kątem jakości i optymalizacji przepustowości. Analiza Offline obejmuje szablon kwalifikacji i weryfikacji pasty lutowniczej oraz dobór jej parametrów. Najlepszym miejscem, aby rozpocząć wdrożenie technologii jest produkcja. Rozpoczyna się od zaprogramowania naszej płytki, co zajmuje około 10 min. Komputer systemowy stworzy dla na wirtualną „golden board”, do której będą porównywane bieżące produkty. System na podstawie pliku Gerber, zawierającego wszystkie informacje o aperturach, tworzy wzorcową, teoretyczną płytkę goden board, łącznie z wysokością depozytu pasty, wyliczoną na podstawie grubości szablonu. W programie można zdefiniować ilość parametrów inspekcyjnych zawierających dopuszczalne wariacje. Typowym parametrem startowym jest minimum 50% i 150% maksimum wysokości szablonu, kalkulacji objętości i 50% przesunięcia pomiędzy środkami pasty i padu. W celu inspekcji jakości drukowania, system skanuje nadrukowane płytki i tworzy dodatkowy model. Około 20 sekund zajmuje odczyt ponad 10 000 depozytów, stworzenia modeli i porównania objętości i lokacji mierzonych depozytów. Jeżeli wszystkie depozyty będą zgodne z założonymi kryteriami system przystąpi automatycznie do kontroli kolejnej płytki. Jednakże w przypadku wystąpienia depozytów nie spełniających założone kryteria system zapisze błąd i poinformuje operatora o znalezionych problemach. Przyczyną wstrzymania kontroli nie musi być koniecznie niedobór pasty lub słaba jakość nadruku – może to być wskazanie zbyt dużej liczby zmian parametrów na płytkach takich jak rozmiary obwodów, lokalizacja i rozmiar padów, zmiany w solder-masce. Podsumowując, inspekcja zakończona niepowodzeniem może być spowodowana złym nadrukiem lub też znacznymi zmianami na samej płytce. Aby rozpoznać przyczynę, operatorzy mogą uruchomić test ponownie, resetując ustawienia płaszczyzny i przeprowadzić test ponownie. Jeżeli weryfikacja zakończy się sukcesem – płytka wraca na produkcję, jeżeli nie to nadruk zostaje zmyty. Jak dużo błędów drukowania jest wykrywanych? To zależy od kompleksowości, zróżnicowaniu i różnic produktu. Rysunek 5 pokazuje odsetek usuwanych nadruków po obu stronach płytki. Mniej skomplikowana dolna strona klasyfikuje się pomiędzy 1 a 2 % błędów.© PBTechnik Rys. 4 Model 3D mierzonego depozytu – wygenerowane przez komputer.
© PBTechnik
Rysunek 5. Procentowe ujęcie błędów usuniętych z linii produkcyjnej.Znacznie bardziej wymagająca strona górna wynosi około 6 do 7% błędów dla aktualnej produkcji przy12% skoku w jednym miesiącu. Gdyby wszystkie wyłapane błędy dostały się na produkcję, to prawdopodobnie wygenerowałyby niesamowite koszty i poważne błędy. Odzyskanie BGA i QFN jest kosztowne i ryzykowne, ale możliwe. Niestety polityka niektórych firm nie pozwala na takie rozwiązania i w przypadku firmy Vicor – te zespoły są złomowane. W takim przypadku niezbędne jest wyłapanie błędów jeszcze zanim powstaną. Jak wygląda sterowanie procesem? Procedury operacyjne są powiązane z błędami. Jeżeli zostanie odnotowane wystąpienie kolejno trzech rzeczywistych błędów – proces jest wstrzymywany i zostaje wezwany zespół specjalistów w celu znalezienia źródła problemu. Co ciekawe, procedury nie wymagają potwierdzenia dobry / zły – rezultat jest oparty tylko i wyłącznie na wskazaniach maszyny. Maszyna jest o wiele dokładniejsza od ludzkiego oka i nie ma najmniejszego sensu opierać się w tym przypadku na dodatkowej opinii operatora, dodatkowo wydłużając proces i zwiększając koszty. Jaki jest końcowy wpływ na naszą linię produkcyjną? Dla firmy Vicor ogólny zysk wzrósł o 3% przy wdrażaniu systemów – jest to znaczny i zauważalny impuls. Dodatkowo zredukowano koszty związane z utylizacją i stratą materiałów. Firma zoptymalizowała też cały proces, co zaowocowało zwiększeniem przepustowości produkcji, eliminacją błędów drukowania i konieczności czyszczenia płytek. Dodatkowo wprowadzono ulepszone procedury ustawiania drukarek – w oparciu o dokładną analizę danych z urządzenia SPI, która odnosi się do wszystkich elementów mających wpływ na jakość nadruku. Jaka jest największa zaleta zdefiniowana przez użytkowników? – kombinacja szybkości i dokładności. Każdy inżynier procesu wie że najważniejsze to znalezienie kompromisu pomiędzy tymi dwoma parametrami – w tym przypadku nie trzeba go szukać. Jaka jest ulubiona aplikacja? Oczywiście „weryfikacja szablonu”. Dzięki tej aplikacji możemy dopuścić szablon do produkcji szybciej i bardziej dokładnie niż kiedykolwiek wcześniej, zachowując możliwość wychwycenia zmian w szablonie (Rysunek 6).© PBTechnik
Rysunek 6. Niewłaściwie wycięty szablon.Następną aplikacją jest DfM, która zapewnia informację zwrotną dla odpowiednich zespołów. Za pomocą tej technologii możemy mieć pewność, że zostaniemy zaalarmowani w przypadku potencjalnych problemów z drukowaniem, jednocześnie zachowując jeszcze czas aby wprowadzić zmiany w produkcie. Również aplikacje offline pozwalają nam na szybką charakteryzację efektywności pasty lutowniczej, przygotowanie i analizie kilku scenariuszy drukowania. Wygenerowane dane pozwalają na zrozumienie wpływu dostawców szablonów, producentów pasty na jakość i koszty w naszej produkcji. Wyobraźcie sobie poprawę efektywności w waszej produkcji o 3% i przeliczcie sami co to może dla was oznaczać – cięcie kosztów, kontrolę kwalifikacji dostawców, wykluczanie błędów już na etapie badania prototypów, jasne wytyczne dotyczące przeglądów i konfiguracji waszych maszyn. Są firmy, w których testowanie wciąż kojarzy się z kosztem, a nie profitem, natomiast problemy są zakopywane przez środki zaradcze, zamiast bezpośrednio usuwane. Pozostaje mieć nadzieję, że rozwój globalnej gospodarki wymusi na wszystkich zmianę sposobu myślenie i będzie korzystny dla wszystkich. Autorem tekstu jest Daniel Trzciński z PB Technik© PBTechnik