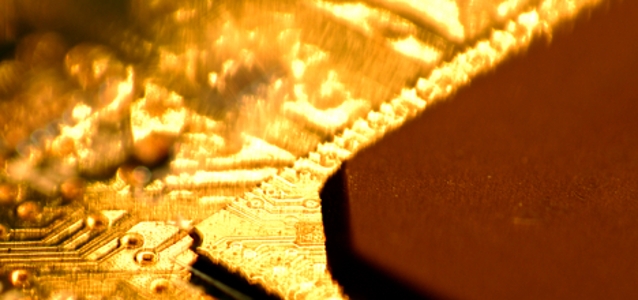
© Grzegorz Wolczyk / Dreamstime
Analizy |
Kontrola procesu w technologii selektywnego conformal coating’u
Ewolucja technologii selektywnego conformal coating’u napędzana jest przez oczekiwania rynku dotyczące ochrony środowiska, coraz większą złożoność układów elektronicznych i zwiększający się poziom automatyzacji.
Surowe standardy jakości
Technologia selective conformal coating’u, czyli selektywnego „lakierowania” układów elektronicznych, cały czas się zmienia; dotyczy to tak maszyn jak i materiałów do zabezpieczania elektroniki. Ewolucja ta jest napędzana przez oczekiwania rynku dotyczące ochrony środowiska, coraz większą złożoność układów elektronicznych i zwiększający się poziom automatyzacji.
Impulsy do rozwoju przychodzą z tradycyjnych rynków, gdzie typowo wymagane jest zabezpieczanie elektroniki, jak motoryzacja, militarny, sprzętu ADG, ale również coraz częściej z rynku medycznego czy urządzeń przenośnych. W niniejszym artykule skupimy się na ważnych wskaźnikach procesu i efektach, które są oczekiwane aby móc mówić w prawidłowym conformal coating’u.
Ciągły nacisk firm na ochronę środowiska oraz wprowadzane regulacje prawne powodują pojawienie się materiałów o mniejszej ilości związków lotnych oraz maszyn zapewniających lepsze panowanie nad płynem, śledzenie i kontrolę procesu. Szczególnie dotyczy to conformal coating’u w samochodowych układach bezpieczeństwa i kontroli trakcji, coraz częściej obecnych w naszym życiu przenośnych urządzeniach elektronicznych czy elektronice medycznej.
To wszystko podnosi standardy i stawia wysokie wymagania wobec kontroli procesu conformal coating’u.
Stopień skomplikowania, przyczyny i efekty, najbardziej przejrzyście oddaje diagram opracowany przez dr. Ishikawę w książce „Guide to Quality Control”. W tej analizie inżynier procesu może zidentyfikować wszystkie czynniki, które wpływają na końcowy rezultat. Diagram powinien być używany jako podstawa do statystycznej kontroli procesu: ustawienia, ograniczenia, monitorowanie kluczowych parametrów dla dalszego ich śledzenia i analizy.
Rysunek: Kontrola procesu
© AMB
Specyfikacje, wymagania.
Dla większości aplikacji conformal coatingu określa się w specyfikacjach następujące wymagania:
1. Strefy i komponenty, które muszą być zabezpieczone.
2. Odporność mechaniczna, odporność na wilgoć, na środowisko chemiczne i inne czynniki występujące w docelowym miejscu użytkowania produktu.
3. Strefy i komponenty, które nie mogą być pokryte, a nawet zabrudzone: złącza, wyświetlacze, pady testowe itp.
4. Kompatybilność chemiczna powłoki z innymi elementami urządzenia lub środowiska (dotyczy to głównie sprzętu medycznego).
5. Rytm pracy, wynikający głównie z szybkości całej linii produkcyjnej.
6. Maksymalna dopuszczalna emisja związków organicznych VOC (Volatile Compound Emissions)
7. Bezpieczeństwo operatora i inne zagadnienia, związane z BHP.
8. Maksymalny dopuszczalny koszt posiadania maszyny czy linii technologicznej.
W zależności od konkretnej aplikacji kolejność, waga każdego z powyższych punktów może być różna. Grubość pokrycia, określenie kształtu pokrycia i wszystkie inne parametry wynikają z powyższych wymagań, a nie stanowią celu samego w sobie!
Po przeanalizowania powyższych wymagań, typowa specyfikacja aplikacyjna zawiera:
1. Typ materiału do pokrywania.
2. Minimalna i maksymalna grubość pokrycia.
3. Kształt pokrycia, z wielkim naciskiem na dystans pomiędzy strefami, które muszą i które nie mogą być pokryte.
Zakładamy, że materiał został dobrany do konkretnej aplikacji oraz właściwie został opracowany proces produkcyjny. Wbrew powszechnej opinii nie jest to proste i aby osiągnąć właściwe rezultaty, nie wpędzając się w kłopoty i ślepe uliczki, pożądana jest ścisła współpraca ze specjalistami w dziedzinie materiałów i maszyn. Po poprawnym ustawieniu procesu, jakość produkcji jest definiowana powtarzalnością kształtu i grubości powłoki oraz jej przyleganiem do powierzchni płytki i komponentów.
Adhezja materiałów jest zależna głównie od przygotowania powierzchni we wcześniejszych procesach i nie jest uwzględniana w niniejszych rozważaniach. Zazwyczaj wystarcza zachowanie odpowiedniej czystości, rzadko wymagane jest mycie płytek. Diagram pokazuje główne zależności przyczyn i efektów wpływających na jakość produkcji. W pewnych sytuacjach pewne czynniki mogą nie mieć miejsca w zależności od materiału i/lub maszyny.
Kontrola procesu
Kontrola procesu właściwie sprowadza się do kontroli czynników, które mogą na niego wpływać, diagram pokazuje główne z nich. Rodzi się pytanie, które z nich i w jaki sposób kontrolować, jak zapewnić stabilną, powtarzalną produkcję? Oto kilka wskazówek:
1. Używanie standardowego sprzętu, z dokumentacją dostępną dla operatorów, aby uniknąć błędnego używania czy ustawiania. W interpretacji „LEAN manufacturing” oznacza to standardową pracę. Przeniesienie na maszynę i oprogramowanie funkcji kontroli i korygowania jak największej części z ustawień jest dobrą strategią na uniezależnienie się od błędów operatora.
2. Monitorowanie kluczowych zmiennych procesu automatycznie lub ręcznie. Automatyczna kontrola daje możliwość logowania zmian, śledzenia i poprawy produkcji.
3. Ustawienie i kontrolowanie limitów dla każdej zmiennej.
4. Automatyczne ostrzeganie kiedy limity zostaną przekroczone, aby uniknąć produkcji wadliwych detali.
5. Używanie zamkniętych pętli sprzężenia zwrotnego dla zmiennych, których z definicji nie da się ustabilizować, czy w inny sposób kontrolować.
Kontrola temperatury płynu
Na diagramie wpływ temperatury płynu widzimy w kilku miejscach. Zmiana temperatury otoczenia powoduje zmianę temperatury płynu i jest odpowiedzialna za zmianę lepkości, przepływu, szerokość wiązki dozowanego materiału, jego czas życia i wreszcie za zwilżanie powierzchni i rozpływ. Każdy z tych czynników wpływa na jakość powłoki; jej kształt i grubość. Najlepiej sprawdza się w tym przypadku stabilizacja temperaturowa płynu z zamkniętą pętlą sprzężenia zwrotnego i recyrkulacją.
Kluczowym parametrem jest lepkość. Szybką i sprawdzoną metodą sprawdzenia lepkości jest używanie kalibrowanych kubków z otworem w dnie. W użyciu jest kilka typów (DIN, ISO, Zahn, Shell), ale najczęściej można spotkać kubek Forda numer 4. Kontrola polega na napełnieniu go płynem i mierzeniu po ilu sekundach materiał wypłynie otworem. Niekiedy sam pomiar może wprowadzić zanieczyszczenia materiału. Stabilizacja temperaturowa wraz z recyrkulacją daje nam pewność, że w każdym momencie produkcji aplikujemy na płytkę materiał o takiej samej lepkości.
Monitoring przepływu płynu
Ilość materiału dozowana na płytkę zależy bezpośrednio od przepływu płynu przez aplikator, oczywiście jeśli maszyny są zdolne do zapewnienia stabilnego przesuwania głowicy dozującej. Przepływ jest bezpośrednio odpowiedzialny za grubość i kształt powłoki. Ze względu na koszt, zakresy, powtarzalność, utrzymanie w ruchu, itp., jest trudno zastosować regulację przepływu w maszynach produkcyjnych. Najlepiej zdaje egzamin zastosowanie przepływomierzy aby go monitorować, logować i alarmować jeśli przekroczy ustanowione limity.
Kontrola ciśnienia materiału
Ciśnienie materiału znajdziemy w kilku miejscach na diagramie, jest jednym z ważniejszych czynników wpływających na efekt końcowy. Większość systemów używa mechanicznych regulatorów ciśnienia jako podstawowej metody kontroli. Zastosowanie elektronicznych regulatorów daje nam możliwość automatycznej regulacji, monitorowania, ostrzegania i umieszczenia tej części kontroli procesu w zadaniach maszyny i oprogramowania. Oprócz uniezależnienia się od możliwych błędów operatora pozwala na zdefiniowanie dla tego samego wyposażenia maszyny różnych konfiguracji, np. szeroka i wąska wiązka materiału z aplikatora.
Kontrola szerokości wiązki
Szerokość wiązki jest zależna od wielu czynników, w większości wynikających z właściwości płynu. Dotyczy to zarówno zatomizowanego spray’u, jak też formowanej bez udziału powietrza kurtyny materiału, tzw. film coater. Szerokość wiązki wpływa głównie na kształt pokrycia, w jakiejś części również na grubość. Najskuteczniej zmieniać szerokość wiązki poprzez zmianę ciśnienia materiału. Zatem, mierząc automatycznie jej szerokość i sprzęgając wynik z odpowiednim ustawieniem ciśnienia płynu, zapewniamy stabilność i powtarzalność produkcji.
Zanieczyszczenia materiału
W wielu przypadkach o zanieczyszczeniu materiału przekonujemy się dopiero kiedy maszyna nie dozuje. Jest wiele przyczyn, od najbardziej oczywistego zanieczyszczenia ciałami obcymi, po częściowo utwardzone drobiny materiału. Każde otwarcie linii materiałowej w maszynie, w tym zbiorników, może spowodować kłopoty. Ważna jest prawidłowa i świadoma obsługa.
Inną ukrytą formą problemów jest stopniowe utwardzanie się materiału z czasem, poprzez odparowywanie rozpuszczalników, powodowane wilgotnością powietrza czy promieniowaniem UV.
Dostawcy materiałów dla zapewnienia jakości stosują znakowanie szarżami, ustanawiają terminy przydatności do użycia, kody kreskowe, moduły RFID lub specjalne opakowania jak bladder bag dla silikonów.
Wpływ operatora
Używanie maszyn do zabezpieczania elektroniki wynika głównie z potrzeby zwiększenia szybkości, wydajności i jakości. Tym niemniej nawet w produkcji automatycznej nie da się uniknąć całkowicie wpływu operatora. Wiele z opisanych już strategii utrzymania jakości, jak kontrola temperatury, ciśnienia, szerokości wiązki, poza bezpośrednim wpływem na proces daje dodatkową korzyść przeniesienia odpowiedzialności z operatora na maszynę i oprogramowanie. W nowoczesnych maszynach od operatora zależy coraz mniej. Oprogramowanie umożliwia na przykład przydzielenie różnych poziomów kontroli maszyny. Logowanie wszystkich czynności maszyny, czy kodów kreskowych z produktów daje możliwość śledzenia i kontroli.
Poza sprawami związanymi bezpośrednio z jakością są należy wspomnieć o:
Wydajność i koszt
Kiedy potrzeba automatyzacji i korzyści z niej płynące dotyczą niemal wyłącznie jakości, to koszty są główną przeszkodą w pełnym zautomatyzowaniu conformal coatingu. Praktycznie każde modele kalkulacji pokazują, że zwiększenie szybkości maszyn zmniejsza koszty posiadania. Prosta kalkulacja, ile sztuk może pokryć maszyna przez czas jej użytkowania, koszt na sztukę produktu i wartość wszystkich wyprodukowanych sztuk pokazuje, że cena zakupu maszyny jest ułamkiem w całkowitych kosztach produkcji. Zaawansowana, szybka maszyna w trochę większej cenie może gigantycznie zmniejszyć koszty produkcji.
Są jeszcze inne wskaźniki, nie tak oczywiste i często pomijane, które potwierdzają korzyści płynące z posiadania szybszych maszyn:
- zwiększenie wydajności poprzez brak poprawek, brak strat,
- zmniejszenie zużycia materiału unikając częstego czyszczenia i ustawiania maszyn,
- zmniejszenie czasu potrzebnego do uruchomienia i kontynuowania produkcji,
- zmniejszenie czasu na przestoje, maintenance.
Troska o środowisko
Conformal coating, jako przemysł, zmienia się pod wpływem regulacji prawnych i ogólnego dążenia do zmniejszenia emisji związków lotnych VOC przez zakłady produkcyjne. Zmniejszenie emisji VOC osiąga się przez zmianę rozpuszczalników na te, które nie podlegają regulacjom prawnym, lub materiałów ze zmniejszoną zawartością VOC, czy wreszcie takich, które mają inne mechanizmy utwardzania.
W pierwszym przypadku opracowuje się nowe formuły materiałów, w tym na bazie wody, co wymaga zmiany procesów w dotychczasowych zastosowaniach. Nowe materiały nie zawsze osiągają takie same parametry jak poprzednie i często nie można ich bezpośrednio zamienić.
Drugie podejście zmniejszenia emisji VOC, polegające na zmniejszeniu ilości tych związków w materiale, jest alternatywnym rozwiązaniem. Zmniejszenie ilości rozpuszczalników zwiększa lepkość materiału, podnosząc wymagania wobec maszyn. Rozwiązaniem może być system recyrkulacji i kontroli temperatury, co czasem daje niespodziewany efekt zwiększenia wydajności maszyn.
Trzecią grupę stanowią materiały o różnych metodach utwardzania, zwane „bezrozpuszczalnikowe”, co oznacza, że nie zawierają związków lotnych. Zazwyczaj do tej grupy należą specyfiki utwardzane światłem UV, pod wpływem wilgoci z powietrza i czasem również utwardzane termicznie. Głównym celem przyświecającym przy opracowywaniu tego typu materiałów było ograniczenie emisji VOC, ale przyniosło to inne korzyści. Otóż formuły utwardzane UV są atrakcyjne tam, gdzie ważny jest czas i/lub miejsce. Zamiast wielu metrów transporterów i energochłonnego pieca można w części tej przestrzeni zmieścić się z szybszym procesem. Rozwiązanie jest szczególnie atrakcyjne dla medycyny i innych aplikacji z racji większej odporności chemicznej tak utwardzanych
materiałów.
Podsumowanie
Proces automatycznego selektywnego conformal coating’u może być ulepszony poprzez odpowiednie strategie kontroli. Zastosowanie ich przyniesie największe korzyści przy współpracy dostawców materiału i maszyn. Owocem technik śledzenia, kontroli i eliminacji źródeł zmiennych w procesie jest polepszenie jakości. Z tego wynika, iż następną korzyścią z dobrej kontroli procesu jest zmniejszenie kosztów posiadania. Maszyna, która kosztowała więcej przy zakupie, może być najmniejszym kosztem w całym cyklu produkcyjnym.
Artykuł, na podstawie materiałów firmy Asymtek, opracowała firma AMB
