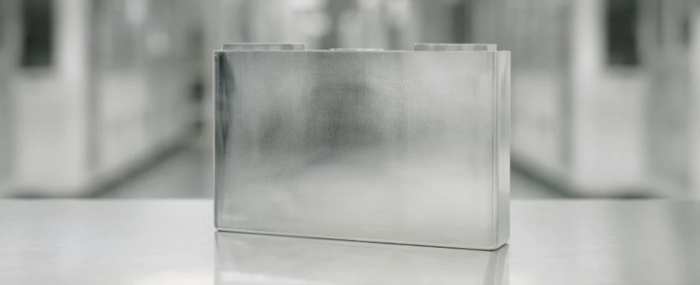
O recyklingu baterii powinniśmy myśleć już na etapie projektowania
Prezes polskiego oddziału Northvolt opowiada nam o działalności firmy w zakresie recyklingu oraz o konieczności ukierunkowania branży akumulatorów na branżę o obiegu zamkniętym.
Według najnowszych danych akumulatory samochodów elektrycznych będą stanowiły 90% rynku baterii litowo-jonowych do 2025 roku, a 11 milionów ton akumulatorów zostanie wycofanych z użytku do końca 2030 roku.
Ignorowanie wartości metali zawartych w bateriach byłoby błędem, ale co gorsza, niepoddanie ich recyklingowi podważyłoby intencje przejścia na pojazdy elektryczne. Ogólnie rzecz biorąc, stoimy w obliczu przyszłości, w której istnieje ogromne zapotrzebowanie na recykling baterii.
Właśnie dlatego rozwój mechanizmów oraz technologii odzysku materiałów zawartych w akumulatorach jest kluczową kwestią, nad którą pracują podmioty publiczne, naukowcy oraz biznes.
O recyklingu rozmawiamy z Robertem Chryc-Gawrychowskim, prezesem polskiego oddziału firmy Northvolt, która wspólnie z firmą Hydro uruchomiła największy zakład recyklingu w Europie oraz buduje zakład recyklingu Revolt na północy Szwecji, który docelowo będzie przetwarzał 125 tysięcy ton zużytych baterii rocznie.
Evertiq: – Co jest obecnie największym problemem w recyklingu baterii?
Robert Chryc-Gawrychowski, Northvolt: – Aktualnie zdecydowana większość baterii oddawanych do recyklingu pochodzi z przenośnych urządzeń elektronicznych, takich jak laptopy czy telefony komórkowe, które są przetwarzane jako odpady elektroniczne. Dostęp do baterii w tych produktach jest stosunkowo prosty z punktu widzenia recyklingu, a ich odzyskiwanie od konsumentów nie jest trudne dzięki istniejącym krajowym programom utylizacji odpadów elektronicznych. Sytuacja jest zupełnie inna w przypadku akumulatorów do pojazdów elektrycznych, które są znacznie większe i bardziej złożone w budowie. Co więcej, Europa po prostu nie wdrożyła jeszcze kompleksowych programów odzysku, które ułatwią skuteczny recykling. Tak więc odzysk baterii z rynku na ten moment jest wyzwaniem dla firm zajmujących się recyklingiem. Właściciele pojazdów elektrycznych nie mogą po prostu wyjąć akumulatora i umieścić go w punkcie zbiórki odpadów elektronicznych.
Wskazane jest zastosowanie rozwiązań cyfrowych, które umożliwią identyfikację i lokalizację baterii pod koniec jej cyklu życia, a także wdrożenie praktycznych rozwiązań w zakresie zbierania i przechowywania baterii przed recyklingiem oraz transportu do stacji recyklingu. Po odzyskaniu pakietów baterii potrzebujemy technologii wspierających wczesne etapy recyklingu, które obejmują na przykład jej rozładowywanie. Świadomość tego typu wyzwań jest ważna i oznacza, że już na etapie projektowania możemy zacząć myśleć o recyklingu akumulatorów.
Kolejnym problemem, który należy wziąć pod uwagę, jest to, że różne firmy stosują różne składy chemiczne w akumulatorach litowo-jonowych, co utrudnia stworzenie znormalizowanej procedury recyklingu.
– Jak projektować akumulatory, żeby jak najłatwiej i najtaniej poddawać je recyklingowi?
– Istotne jest, aby projektować akumulatory pod kątem obiegu zamkniętego na trzech poziomach: komponentów, ogniw i systemów. Baterie powinny być przede wszystkim łatwe do usunięcia z produktu i do demontażu na mniejsze części. Dzięki ograniczonej złożoności etapów montażu możliwe jest zastosowanie automatyzacji, która obniża koszty całego procesu.
Jeżeli spojrzymy na konstrukcje systemów bateryjnych, to demontaż ułatwia zmniejszenie ilości kleju i kabli stosowanych w produkcie. Szczególne znaczenie ma również rodzaj połączeń między modułami i poszczególnymi ogniwami – standaryzacja tych połączeń minimalizuje liczbę czynności i wykorzystywanych narzędzi.
– Czy recykling się opłaca?
– Pozyskiwanie surowców do produkcji baterii poprzez recykling stanowi ogromną szansę. W porównaniu z wydobyciem metali jest to tańsza, bardziej zrównoważona i bezpieczniejsza opcja. I chociaż recykling już dziś ma sens, to jego znaczenie i opłacalność będą wzrastały wraz z intensyfikacją globalnej produkcji baterii i zależności społeczeństwa od metali.
– Jak dużą część materiałów akumulatorowych jesteśmy w stanie odzyskać przy obecnych technologiach produkcji i recyklingu?
– 95% materiałów znajdujących się w bateriach można odzyskać i poddać recyklingowi. Intencją programu recyklingowego Northvolt jest maksymalizacja odzysku materiałów wysokiej jakości przy użyciu metod, które minimalizują wpływ recyklingu na środowisko.
Dużą wartość stanowią odzyskane metale, w tym miedź, aluminium i stal oraz materiały aktywne znajdujące się w elektrodach: nikiel, kobalt, lit i mangan. Z chemicznego punktu widzenia metale pochodzące z recyklingu są funkcjonalnie identyczne z metalami pochodzącymi z górnictwa. Z tego powodu możemy ukierunkować branżę akumulatorów na branżę o obiegu zamkniętym – przemysł, który odzyskuje swoje produkty z rynku do recyklingu i wprowadza odzyskane materiały z powrotem do procesów produkcyjnych nowych baterii.
– Czy działalność firmy Northvolt w obszarze recyklingu obejmuje/będzie obejmowała same ogniwa, czy też całe systemy bateryjne (elektronikę, kable, etc.)?
– Działalność Northvolt w zakresie recyklingu obejmuje całe systemy bateryjne, które są demontowane co najmniej do poziomu modułu bateryjnego. W tym celu stosowane są wysoce zautomatyzowane maszyny, wykorzystujące inteligentne oprogramowanie do identyfikacji modeli akumulatorów, ułatwiając w ten sposób ich demontaż i recykling.
Demontaż pozwala na odzyskanie stalowych obudów, miedzianych szyn zbiorczych i okablowania, a także tworzyw sztucznych i innej elektroniki, które oddajemy do zewnętrznego recyklingu. My skupiamy się natomiast na recyklingu ogniw i odzysku litu, niklu, manganu i kobaltu.
– Działa już zakład recyklingu Hydrovolt w Norwegii, ale wiadomo, że liczba akumulatorów, które będzie trzeba przetworzyć będzie szybko rosła w nadchodzących latach. Jakie są dalsze plany firmy Northvolt w tym zakresie?
– Naszym celem jest pozyskiwanie 50% metali do produkcji ogniw bateryjnych z recyklingu do 2030 roku. Do tego czasu moc produkcyjna w naszych gigafabrykach wzrośnie do 150 GWh rocznie, co pozwoli na dostarczenie pakietów bateryjnych do 2,5 miliona aut. To ambitny cel i aby odnieść sukces, potrzebujemy zakładów recyklingu działających na skalę przemysłową.
Pierwszym krokiem było wspólne przedsięwzięcie Northvolt i Hydro o nazwie Hydrovolt, dzięki któremu powstał największy w Europie zakład recyklingu akumulatorów. Znajduje się w Norwegii, kraju, który jest liderem w korzystaniu z samochodów elektrycznych. Hydrovolt może przetworzyć 12 000 ton zestawów akumulatorów rocznie, co odpowiada około 25 000 pojazdów elektrycznych. To wystarczy do recyklingu całej rocznej ilości zużytych akumulatorów w Norwegii.
Zakład recyklingu (Revolt Ett) budujemy również w Szwecji, zaraz obok gigafabryki Northvolt Ett. Będzie przetwarzał około 125 000 ton zużytych baterii rocznie i zdecydowanie będzie to największy tego typu zakład recyklingu na świecie.
Recykling nie jest jedynym składnikiem, który zapewnia zrównoważony rozwój branży akumulatorów. Ważny jest zrównoważony proces produkcji, wykorzystujący energie odnawialną, zasilającą nasze zakłady. Jednak jest kluczowym dopełnieniem układanki – takim, który w znacznym stopniu przyczyni się do zmniejszenia środowiskowych kosztów produkcji akumulatorów, a ostatecznie całej rewolucji związanej z elektromobilnością. Co więcej, w recyklingu baterii znajdujemy okazję do zademonstrowania, w jaki sposób i dlaczego cyrkularność musi stać się podstawową cechą wszystkich branż produkcyjnych.
– Dziękuję za rozmowę!
Northvolt to europejski dostawca ogniw i systemów bateryjnych. Firma została założona w 2016 roku z misją budowy najbardziej ekologicznej baterii na świecie o minimalnym śladzie węglowym i najwyższych możliwościach recyklingu. Northvolt zatrudnia ponad 3000 pracowników 110 różnych narodowości.
Od 2018 firma funkcjonuje w Polsce pod nazwą Northvolt Poland Sp. z o.o. Spółka została zawiązana, aby sprostać rosnącemu zapotrzebowaniu na kompletne systemy bateryjne. W zakładzie w Gdańsku produkuje systemy magazynowania energii oraz moduły bateryjne zastępujące silniki spalinowe w maszynach wykorzystywanych w przemyśle. Obecnie firma Northvolt Poland zwiększa swoje zdolności produkcyjne, inwestując w Gdańsku 200 mln USD w budowę zautomatyzowanego zakładu produkcyjnego o powierzchni 50 tysięcy m kw. Dzięki temu powstanie 500 nowych miejsc pracy.