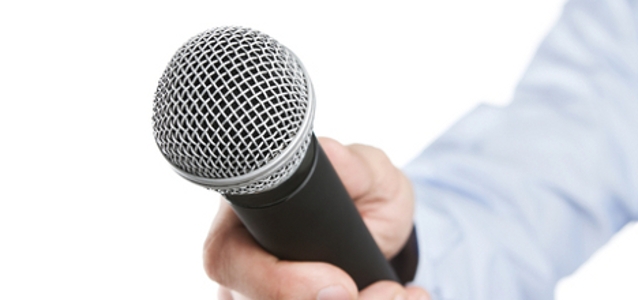
© rangizzz dreamstime.com
Przemysł elektroniczny |
Elgór+Hansen zwiększa moce produkcyjne
Producent elektroniki dla górnictwa we wrześniu tego roku zakończył reorganizację działu produkcji elektroniki, wdrażając nowe maszyny i system traceability.
Wchodząca w skład Grupy Kapitałowej FAMUR chorzowska firma Elgór+Hansen ma długą historię, której początek sięga 1945 roku, kiedy to działalność rozpoczęła Spółdzielnia Pracy „Radiotechnik” w Katowicach, produkująca m.in. odbiornik „Karlik”. Przez lata zmieniała się struktura firmy i zakres świadczonych usług. Obecnie spółka koncentruje się na kompleksowej ofercie w zakresie szeroko rozumianej elektrotechniki i automatyki. O ostatnich inwestycjach w park maszynowy, które zapewniły firmie gotowość do świadczenia usług montażu kontraktowego, opowiada Tomasz Grzyśka, wiceprezes zarządu ds. rozwoju w firmie Elgór+Hansen SA.
evertiq.pl: – Czym zajmuje się Elgór+Hansen?
Tomasz Grzyśka, wiceprezes zarządu ds. rozwoju w firmie Elgór+Hansen SA: – Elgór+Hansen projektuje oraz produkuje aparaturę elektryczną zasilającą oraz łączeniową do zasilania maszyn stosowanych w górnictwie. Prowadzimy pełną obsługę inwestycji w zakresie projektowania, produkcji, serwisu i remontu urządzeń budowy przeciwwybuchowej. Ponadto dostarczamy całościowe rozwiązania w zakresie zintegrowanych systemów zasilania i sterowania kompleksami wydobywczymi. Wdrażamy także rozwiązania z zakresu informatycznych systemów nadzoru pracy maszyn i urządzeń.
Elektronikę na własne potrzeby produkujemy od 25 lat. Mamy wysokie kompetencje w zakresie projektowania i produkcji podzespołów do pracy w trudnych warunkach środowiskowych oraz wymagających certyfikacji zgodnej z dyrektywą ATEX, przeznaczonych do stref zagrożonych wybuchem.
W trakcie rozpoczętego w 2017 roku procesu integracji Grupy FAMUR z Grupą KOPEX, działalność w zakresie projektowania i produkcji urządzeń elektronicznych została skupiona w naszej spółce. Mieliśmy największe doświadczenie w tym obszarze, stąd była to słuszna decyzja, która poskutkowała skokowym wzrostem produkcji związanym z zapewnieniem dostaw dla całej Grupy.
– Skąd potrzeba inwestycji w maszyny do produkcji elektroniki?
– Inwestycja w nową linię i system traceability okazała się niezbędna, aby zapewnić wysoki poziom jakości i niezawodności dostarczanych przez nas podzespołów. Dzięki temu znacząco zwiększyliśmy nasze moce produkcyjne, co z kolei pozwoliło na większą aktywność w poszukiwaniu zleceń poza Grupą. Nasze doświadczenie pozwala nam zaoferować wysokiej jakości usługę montażu, nie tylko kontraktowego, ale również kompleksowego, wspartego usługą projektowania.
To, co nas wyróżnia, to właśnie automatyczny systemem traceability. Możemy śledzić dowolny element w cyklu życia produktu, od momentu dostawy do momentu jego utylizacji. Mamy pełną wiedzę na temat tego, w jakich urządzeniach został zamontowany dany element, z jakimi parametrami została nałożona pasta lutownicza, jakie parametry były ustawione na piecu rozpływowym czy jaki był wynik automatycznej kontroli optycznej. Ta funkcjonalność jest dla nas niezwykle istotna. Produkujemy podzespoły do maszyn, które niejednokrotnie ważą po kilkadziesiąt ton i pracują kilka czy kilkanaście tysięcy kilometrów stąd. Musimy więc mieć możliwość odpowiedniego reagowania na usterki.
– Jakie nowe urządzenia kupiła firma?
– Jeśli chodzi o ostatnie inwestycje, to przede wszystkim zakupiliśmy nową linię do produkcji elektroniki. Dokonaliśmy także gruntownej przebudowy i reorganizacji wydziału odpowiadającego za produkcję urządzeń elektronicznych. Istotne elementy inwestycji to automatyczna sitodrukarka z inspekcją 3D firmy ERSA, dwa automaty pick & place, pracujące w linii firmy ESSEMTEC oraz piec rozpływowy siedmiostrefowy firmy ERSA. Ponadto zaopatrzyliśmy się w automatyczny magazyn elementów firmy ESSEMTEC, urządzenie do automatycznej inspekcji optycznej AOI firmy KOHYOUNG, urządzenie myjące firmy PBT WORKS, a także automat do lutowania selektywnego firmy ERSA.
Linia została skonfigurowana w taki sposób, aby zapewnić jak najkrótszy czas przezbrojeń pomiędzy realizowanymi projektami. Biorąc pod uwagę różnorodność produkowanych przez nas podzespołów, było to kluczowe z punktu widzenia efektywności. Pełną zdolność produkcyjną osiągnęliśmy pod koniec września 2020 roku. W obliczu obecnej sytuacji epidemiologicznej dotrzymanie terminu realizacji było bardzo dobrym osiągnięciem.
System traceability wdrażano jednocześnie z linią produkcyjną, a więc pod koniec września mogliśmy już korzystać z jego pełnej funkcjonalności. Co ważne, system działa w pełni automatycznie na linii produkcyjnej i pozwala również na śledzenie elementów dokładanych na ręcznych stanowiskach montażu, a także w trakcie prac serwisowych. To efekt bardzo dobrej współpracy z dostawcą, który spełnił wszystkie nasze oczekiwania w tym obszarze. Dzięki temu powstały rozwiązania, które są unikalne w naszym regionie.
– Czy planowane są kolejne inwestycje?
– Wystarczająco zwiększyliśmy moce produkcyjne i na tyle poprawiliśmy efektywność, że w najbliższym czasie nie planujemy znaczących inwestycji w tym obszarze. Chcemy jednak uzupełnić wydział o kolejne pojedyncze urządzenia, które w innych procesach pozwolą zwiększyć efektywność i jakość.
– Ile osób pracuje w firmie Elgór+Hansen?
– Aktualnie w firmie pracuje 240 osób. Co warte podkreślenia, produkcja elektroniki to tylko mniejsza część naszej działalności. Posiadamy liczny dział rozwoju zajmujący się opracowywaniem nowych rozwiązań z zakresu zasilania, sterowania i wizualizacji. Zespół składa się z inżynierów o wielu różnych specjalnościach. Wśród nich są: konstruktorzy elektrycy, konstruktorzy elektronicy, konstruktorzy mechanicy, programiści czy też specjaliści w zakresie certyfikacji na rynki europejskie i rosyjskie.
Firma przez ostatnie dwa lata mocno się rozwijała, co poskutkowało około 30% wzrostem zatrudnienia. Nieustająco jednak poszukujemy nowych talentów.
– Jaka część produkcji elektroniki realizowana jest na potrzeby Grupy FAMUR, a jaką część stanowi produkcja w ramach montażu kontraktowego?
– Po osiągnięciu pełnej funkcjonalności linii, tj. od września 2020 roku, cała nasza produkcja jest realizowana dla Grupy. Ostatnie miesiące to czas zapoznawania się z parkiem maszynowym, szkolenia załogi, wdrożenia kultury organizacji Lean Management oraz uzyskania certyfikatów IPC. Dzięki temu obecnie jesteśmy w pełni gotowi do przyjmowania zleceń w zakresie montażu kontraktowego.
– Dziękuję za rozmowę!