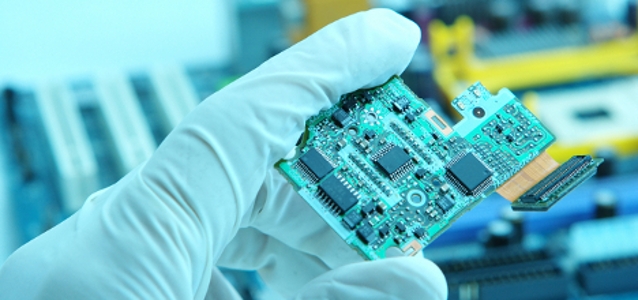
© andrey burmakin dreamstime.com
Analizy |
Redukcja poziomu pustek lutowniczych w procesie lutowania w oparach
Technologia lutowania w oparach staje się coraz popularniejsza, szczególnie w sytuacjach gdzie spotykamy się z produkcją high mix low volume, prototypowaniem lub lutowaniem produktów w których występują komponenty o dużej różnicy pojemności cieplnej (duże stalowe złącza i małe elementy np. 0201).
Czasem polutowanie takiej płytki w piecu rozpływowym jest wręcz niemożliwe, natomiast bez trudu wykonalne w piecu kondensacyjnym, poprzez proste wykorzystanie praw fizyki, gdy gorące opary (200 – 2600C) kondensują się na lutowanym układzie. Temperatura lutowania jest zależna od temperatury wrzenia czynnika (Galdenu). W zależności od tego jaki zostanie zastosowany Galden, osiągniemy różne temperatury pary, z której ciepło zostanie przetransferowane do spoiwa. Ponieważ opary kondensują się na całej powierzchni płytki mamy pewność, że proces jest całkowicie beztlenowy. Dodatkowo mamy pewność, że nie przekroczymy temperatury wyższej niż temperatura wrzenia wybranego typu Galdenu. Cały proces można przedstawić w czterech etapach.
I etap – Galden jest podgrzewany i zaczyna parować
II etap – płytka jest zanurzona w oparach, które się na niej kondensują i przekazują ciepło w następstwie czego dochodzi do lutowania
III etap – płytka, elementy i spoiwo osiąga temperaturę wrzenia czynnika (Galdenu)
IV etap – płytka jest wyciągana z komory lutującej i następuje jej chłodzenie.
Sama technologia ma mnóstwo zalet, takich jak niskie zużycie energii, łatwość profilowania, brak efektu cienia, szybka gotowość urządzenia do pracy. Niestety samo lutowanie w oparach nie obniża znacznie poziomu pustek lutowniczych, choć jest ich nieco mniej niż po lutowaniu w piecach rozpływowych.
Dlatego kolejnym etapem rozwoju tej technologii jest zastosowanie komory próżniowej, która z łatwością pozwoli nam osiągnąć ilość pustek lutowniczych (voids) poniżej 5%. Jeśli chodzi o usuwanie tego problemu, próżnia jest obecnie najlepszym rozwiązaniem w przeciwieństwie do zastosowania wibracji (możliwość fizycznego uszkodzenia niektórych elementów ) lub do zwiększania ciśnienia co finalnie skutkuje zwiększeniem naprężeń w spoiwie.
Naturalnym jest, że wymagania produkcyjne rosną wraz z czasem i dlatego kolejnym etapem jest osiągnięcie poziomu pustek lutowniczych poniżej 1 % co z łatwością można osiągnąć stosując procedurę Multi Vacuum opracowaną przez ASSCON. Na poniższym zdjęciu widać jak wygląda spoiwo po procesie Multi Vacuum z poziomem voidsów poiniżej 1%
Tak niski poziom pustek lutowniczych można osiągnąć poprzez trzykrotne zastosowanie próżni w procesie lutowania. Tak jak widać na poniższym wykresie, próżnia (0.5 mbar) występuje przed rozpoczęciem nagrzewania, co eliminuje pęcherze powstałe w trakcie nakładania spoiwa, następnie występuje podwójny cykl próżniowy w fazie płynnej spoiwa.
Do niedawna znaczącymi ograniczeniami tej technologii była wydajność, natomiast w chwili obecnej inline’owe piece kondensacyjne z próżnią są nawet nieco szybsze niż ich odpowiedniki w technologii rozpływowej. Piece kondensacyjne z próżnią są tańsze w zakupie i eksploatacji. Powyższe zalety technologii Vapor Phase i jej przewaga nad technologią lutowania rozpływowego powoduje, że jest najczęściej wybieranym rozwiązaniem w sytuacjach gdzie zachodzi potrzeba znacznego obniżenia poziomu pustek lutowniczych. Najczęstsze zastosowanie technologia ta znajduje w branży automotive, militarnej i oświetleniowej.
Autor:
Grzegorz Kopczyński
© Amtest Poland
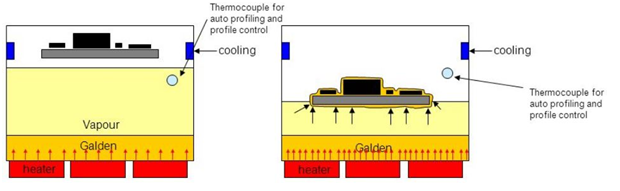
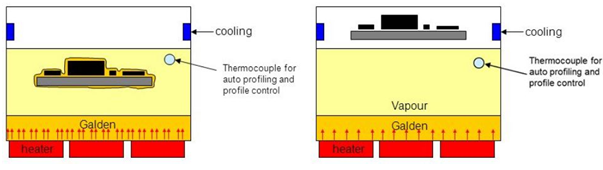
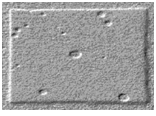
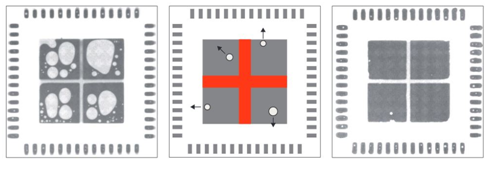
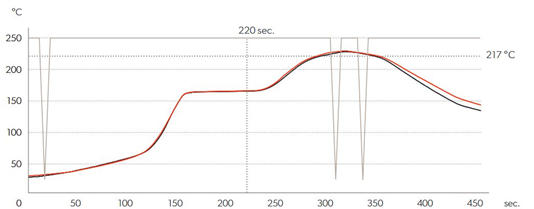