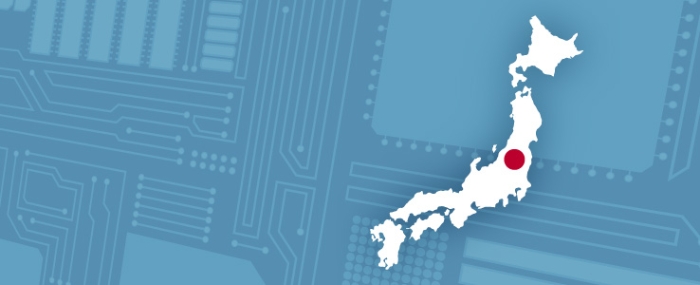
Rewolucja w mikroskali: najcieńsza i najbardziej złożona płytka PCB od OKI
W świecie miniaturyzacji elektroniki i coraz większych wymagań technologicznych granice możliwości są stale przesuwane. Najnowszym tego przykładem jest osiągnięcie japońskiej firmy OKI Circuit Technology, która opracowała płytkę drukowaną (PCB) zawierającą aż 124 warstwy – to największa liczba warstw używana w zastosowaniach komercyjnych związanych z testowaniem układów półprzewodnikowych.
To ogromny przełom, który może znacząco wpłynąć na rozwój sztucznej inteligencji, technologii obronnych, lotnictwa czy systemów komunikacyjnych nowej generacji.
Dlaczego liczba warstw ma znaczenie?
W każdej płytce PCB znajdują się warstwy przewodzące prąd, odpowiadające za przesyłanie sygnałów i zasilanie komponentów. Im więcej warstw, tym więcej połączeń można zmieścić w ograniczonej przestrzeni, a to oznacza większą moc obliczeniową, lepszą kontrolę nad sygnałem i możliwość obsługi zaawansowanych protokołów komunikacyjnych, takich jak PCIe Gen6 czy CXL 3.0.
Dotychczas technologicznym szczytem były konstrukcje 108-warstwowe, a przekroczenie tej granicy stwarzało problemy natury mechanicznej i termicznej – płytki stawały się zbyt grube, podatne na uszkodzenia i trudne do wyprodukowania. OKI udało się uzyskać 124 warstwy, zachowując jednocześnie standardową grubość 7,6 mm – to jak zbudować 124-piętrowy wieżowiec na fundamencie zaprojektowanym na 100 pięter.
Jak to możliwe?
Sukces OKI opiera się na wielu usprawnieniach technologicznych. Firma wykorzystała ultracienkie materiały dielektryczne – zaledwie 25 mikrometrów grubości na warstwę – które dobrze przewodzą ciepło i nie zakłócają sygnałów nawet przy częstotliwościach powyżej 100 GHz. Prawdopodobnie użyto tu specjalistycznych laminatów, takich jak Megtron 7.
Dzięki takiej budowie możliwe jest testowanie nowoczesnych układów pamięci HBM (High Bandwidth Memory), które są kluczowe w akceleratorach AI. Zwiększona liczba warstw umożliwia też dodanie większej liczby płaszczyzn uziemiających i trasowanie sygnałów z dużą precyzją – bez ryzyka zakłóceń czy przegrzania.
Wysoka cena przełomu
Oczywiście, każda innowacja ma swoją cenę. Produkcja jednej płytki o powierzchni metra kwadratowego kosztuje ponad 4 800 dolarów, a czas realizacji to nawet 16 tygodni. Co więcej, tylko około 65% z nich przechodzi kontrolę jakości – to mniej niż w przypadku starszych technologii, gdzie współczynnik ten sięga 85%.
Dodatkowym wyzwaniem są naprężenia mechaniczne pojawiające się podczas pracy – mogą one prowadzić do uszkodzeń, często trudnych do wykrycia i naprawy, szczególnie w środkowych warstwach płytki.
Co dalej?
Na razie 124-warstwowe płytki znajdą zastosowanie głównie w niszowych, bardzo zaawansowanych projektach. Jednak technologie, które umożliwiły ich powstanie, z czasem mogą trafić do masowej produkcji – zwłaszcza gdy rozwój narzędzi wspomaganych sztuczną inteligencją i produkcji przyrostowej (druk 3D elektroniki) staną się bardziej opłacalne.
Choć rekord świata, ustanowiony przez japoński koncern Denso w 2012 roku i wynoszący 129 warstw, wciąż pozostaje niepobity, to OKI swoim osiągnięciem udowodniło, że da się projektować ekstremalnie złożone płytki bez odchodzenia od standardów produkcyjnych. A to może być krok milowy ku przyszłości, w której potężne układy obliczeniowe zmieszczą się w kieszeni.