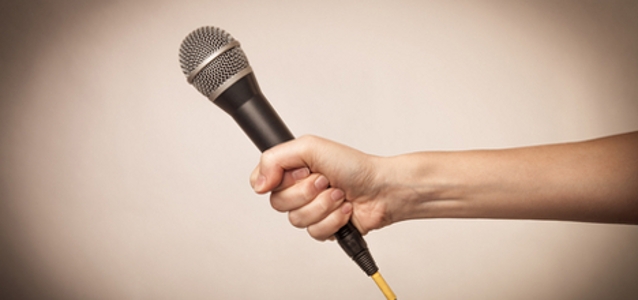
© beatricee _dreamstime.com
Przemysł elektroniczny |
Wykład NCAB Group Polska na TEC Warszawa 2016
Co prawda w wielu urządzeniach nadal najlepiej sprawdzą się tradycyjne, sztywne PCB, ale giętkie płytki coraz częściej pojawiają się w zaawansowanych technologicznie produktach dostępnych na sklepowych półkach.
„Technologia Hot Bar wraz z płytkami flex – budowa, zastosowania, korzyści” to temat wykładu, który podczas targów elektronicznych TEC Warszawa 2016 poprowadzą dwaj eksperci: Michał Kopcewicz z firmy NCAB oraz Marek Bernaciak z AMB Technic. Dzisiaj zachęcamy do wywiadu z Michałem Kopcewiczem na temat płytek flex, a już niedługo zaprosimy do rozmowy na temat technologii Hot Bar.
Przede wszystkim jednak zachęcamy do bezpłatnej rejestracji na tegoroczny TEC Warszawa przez naszą stronę internetową.
evertiq.pl: Płytki giętkie – czy to jeszcze nisza, czy już część głównego nurtu elektroniki?
Michał Kopcewicz, NCAB: - Płytki giętkie znajdują się w zaawansowanych technologicznie produktach, w których trzeba upakować wiele elementów, połączeń na małej lub powyginanej przestrzeni. Są to np. opaski na rękę, aparaty fotograficzne czy bardziej skomplikowane urządzenia w samolotach czy samochodach.
Giętkie płytki stosuje się przede wszystkim w nowoczesnych aplikacjach, widać je w najnowszych trendach w elektronice, mówimy tu o elektronice użytkowej, ubieralnej, czyli chociażby produktach dla branży fitness lub medycznej.
Można więc powiedzieć, że na świecie zastosowanie płytek flex jest już powszechne. Przydają się wszędzie tam, gdzie trzeba miniaturyzować urządzenia lub ich kształt jest specyficzny. Zapotrzebowanie na elastyczne płytki na pewno będzie rosło, ale część prostych produktów pozostanie przy tradycyjnych PCB.
- A jak wygląda sytuacja w Polsce?
- Jesteśmy dopiero na początku wprowadzania tej technologii do naszego przemysłu elektronicznego. Konsumenci w Polsce używają produktów, w których montowane są płytki flex, jednak w naszym kraju nie ma fabryki, która produkuje takie komponenty. Płytki flex są zamawiane, głównie z Azji. Natomiast jeśli chodzi o montaż – to tak, są firmy które się tym zajmują.
Obserwujemy, że coraz więcej zaawansowanych produktów przychodzi do Polski i są tu montowane, ale to wciąż ułamek procenta w stosunku do całości produkcji. Na naszym rynku mamy przewagę produkcji prostych lub średniozaawansowanych urządzeń, a skomplikowane technologie często zatrzymywane są w krajach Europy Zachodniej. Tamte firmy mają większe doświadczenie, tymczasem u nas wciąż brakuje ekspertów w dziedzinie produkcji elektroniki high-tech, co ogranicza przerzucanie skomplikowanych projektów do Polski. Na szczęście to się zmienia, przykładowo firmy EMS mają coraz częściej świetnych ekspertów, ale na widoczne efekty pod tym względem trzeba czekać latami.
- Przejdźmy zatem do zalet płytek flex.
- Dają możliwość upakowania elektroniki na małej, wymaganej przestrzeni, bez kabli, konektorów, dostosowują się do pożądanego kształtu produktu końcowego. Możemy skonstruować urządzenia o niestandardowych, nawet dziwacznych kształtach. Drugi ważny plus to znaczna redukcja wagi – bez kabli i konektorów, a co za tym idzie komfort użytkowania przez konsumenta. Benefity produkcyjne to redukcja czasu ze względu na montaż komponentów w jednym procesie, redukcja etapów montażu, testowanie pełnej aplikacji w jednym procesie. Otrzymujemy zatem produkt mniejszy, lżejszy, lepiej zaprojektowany i szybciej wyprodukowany.
- Jakie są bariery w rozwoju tej technologii?
- Przede wszystkim są to przeszkody technologiczne od strony fabryk. Wymagana jest specjalna technologia produkcji, więc nie wszystkie fabryki mogą sobie pozwolić na dostarczanie płytek flex. Do tego dochodzi np. kwestia utrzymania odpowiednich tolerancji.
Druga bariera to możliwości projektowe – chodzi o designerów, którzy się tym zajmują. Na tym polu potrzeba jeszcze nauki i doskonalenia, żeby umieć taką płytkę zaprojektować. Są oczywiście kraje w których te technologie są stosowane od kilku lat i tamtejsze biura projektowe robią to powszechnie, ale jeśli chodzi o Polskę to cały czas jesteśmy na początkowym etapie tych działań.
Płytki giętkie kosztują też więcej niż standardowe PCB. W tym przypadku klient powinien sobie przeanalizować, czy jednak warto zastosować płytkę typu flex w jego produkcie końcowym, bo może się okazać, że osiągnie przez to przewagę konkurencyjną, która zrekompensuje wyższe koszty produkcji.
- Czy firma NCAB, jako producent PCB, rozwija działalność związaną z płytkami flex?
W Polsce nie produkujemy takich płytek, ale są klienci, którzy je zamawiają. Natomiast jako Grupa ciągle szukamy nowych fabryk. Nasz sourcing w Azji i w Europie prężnie działa, oceniamy sytuację na podstawie tendencji na rynku lub zapotrzebowania w danym kraju i poszukujemy odpowiednich zakładów. Niedawno zaaprobowaliśmy fabrykę, z którą współpracujemy już w zakresie płytek sztywnych, do produkcji elastycznych. Fabryki też zauważają większe zainteresowanie na rynku i rozbudowują swoje linie produkcyjne, więc i my zwiększamy moce przerobowe.
- Dziękuję za rozmowę!