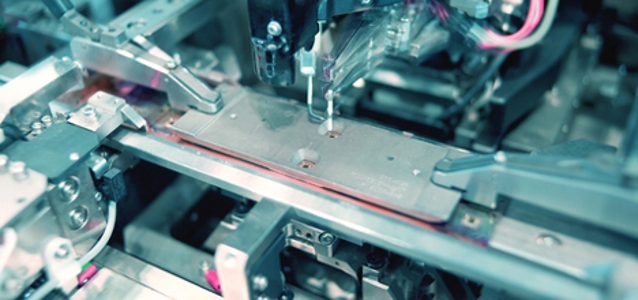
© pengyou93 dreamstime.com
Analizy |
Procesy dozowania i pokrywania w przemyśle fotowoltaicznym
Wraz z wieloma innymi zadaniami, utrzymanie kosztów produkcji na niskim poziomie przy zachowaniu odpowiedniej jakości, jest jednym z ważniejszych wyzwań w przemyśle produkcji i montażu ogniw solarnych. Mając na uwadze niewątpliwe podobieństwa z przemysłem półprzewodników, można stwierdzić, iż przemysł fotowoltaiczny znajduje się w przełomowym punkcie rozwoju jeśli chodzi o metody produkcyjne.
W miejsce pracy manualnej i małych partii produkcyjnych wchodzą zautomatyzowane procesy produkcji. Aby produkować po niskich kosztach moduły o wysokiej efektywności, należy redukować koszty materiałów, optymalizować procesy produkcyjne oraz jednocześnie podnosić ich niezawodność i trwałość.
W wielu przypadkach, w przemyśle fotowoltaicznym można zaimplementować wprost rozwiązania sprawdzone przy produkcji elektroniki czy półprzewodników. Eliminuje to konieczność opracowywania nowych metod, wraz z ich wysokimi kosztami oraz ryzykiem nierozerwalnie związanym z procedurami ‘specjalnymi’. Przykładowo, selektywne pokrywanie ochronne przed dłuższy już czas z sukcesem jest stosowane w przemyśle elektronicznym czy motoryzacyjnym w celu ochrony wrażliwej elektroniki przed przedwczesna awarią, spowodowaną wpływem warunków zewnętrznych, takich jak wilgotność, zmiany temperatury, zanieczyszczenia itp.
Podobnie wysokie wymagania w przemyśle fotowoltaicznym stawia sie przed inwerterami, które mają wysoki wpływ na efektywność systemu. Poza efektywnością, najważniejszym aspektem całego systemu jest też jego niezawodność. Koszt produkcji energii słonecznej wciąż jest relatywnie wysoki I w związku z tym zwrot z inwestycji to obecnie wiele lat. Systemy precyzyjnego pokrywania mogą zredukować koszty ze względu na zwiększoną niezawodność i jakość, które wnoszą do procesu produkcji fotowoltaiki. Dodatkowo, oferują one również przewagę wydajności i powtarzalności, jakie może zapewnić zautomatyzowany system, a także mogą być łatwo dostosowywane do wielkości procesu, od niewielkich partii do produkcji masowej.
Pokrywanie ochronne
W celu poprawy odporności systemów wytwarzania energii solarnej, niezbędna jest zarówno redukcja kosztów, jak I poprawa niezawodności. Kluczową rolę w zapewnieniu długowieczności I efektywności odgrywają inwertery, które jednak są narażone na intensywne oddziaływanie warunków klimatycznych. Poprzez pokrywanie inwertera warstwami ochronnymi, znacznej poprawie ulegają właściwości dielektryczne, odporność mechaniczna czy odporność na przebicia. Pokrywanie ochronne zapewnia dodatkową ochronę przeciwko przedwczesnym awariom, spowodowanym takimi czynnikami jak wilgotność, migracja, skażenia czy inne zanieczyszczenia.
Warunki wytwarzania wymagają aplikacji warstwy o jednorodnej grubości oraz wytwarzania jej w sposób całkowicie powtarzalny, a także pokrywania selektywnego. Systemy pokrywania Nordson Asymtek dzięki rozwiniętym systemom regulacji procesów posiadają możliwości aplikacji powłok ochronnych w sposób automatyczny oraz selektywny, w krytycznych obszarach inwertera. Pozwala to zapewnić znacznie wyższą niezawodność, pozwalając na dłuższy okres użytkowania urządzenia, redukując koszty i przestoje, a w efekcie zwiększając efektywność systemu solarnego.
Całościowe rozwiązania
W szczególności przydatne w opisywanych aplikacjach są zawory jet, wykonujące pokrywanie bezkontaktowe, podobnie jak drukarki atramentowe. Stosując modulowany rytm pracy, wraz z możliwościami kontroli, osiągnięto wysoką elastyczność procesu. Możliwe jest przesunięcie zaworu do zdefiniowanej pozycji, zatrzymanie oraz aplikacja płynu na zaplanowanej, małej przestrzeni i osiągnięcie najwyższego stopnia selektywności. Dzięki kontroli impulsów, rozmiar kropli i jej grubość mogą być dostosowywane do indywidualnych potrzeb.
Jetting umożliwia ponadto pokrywanie skomplikowanych geometrycznie kształtów, tworzenie linii, czy pokrywanie znacznych powierzchni z większą szybkością. W tych przypadkach zawór jest sterowany ze stałą prędkością i pracuje z zaplanowaną częstotliwością, według stałej, wcześniej zaplanowanej trasy, nie wchodząc w kontakt z poszczególnymi punktami na powierzchni PCB. Średnica punktów oraz odstęp pomiędzy nimi ustala się za pomocą odpowiedniego oprogramowania, tak aby poszczególne punkty nie stykały się ze sobą, tworząc jednocześnie jednolitą warstwę ochronną.
Należy też wspomnieć o innych, wcześniejszych etapach procesu produkcyjnego ogniw fotowoltaicznych, w których niezbędne jest dozowanie płynów przy zachowaniu najwyższej precyzji. Przykładem może być dozowanie klejów przewodzących, tworzących ciągi przewodzące. Poprzez selektywne nałożenie topnika w systemie jet, również samo lutowanie może odbywać się w sposób zapobiegający powstawaniu zanieczyszczeń, zwiększając niezawodność punktu lutowniczego. W komórkach koncentratora, w efekcie zastosowania coatingu, chroniona jest powierzchnia półprzewodnika, co podnosi efektywność system. Dzieję się tak ze względu na ochronę wrażliwych powierzchni przed ciepłem generowanym w efekcie koncentracji promieni słonecznych w soczewce. Również materiał półprzewodnikowy w koncentratorze mocowany jest specjalnym klejem.
Wybór odpowiedniego materiału ciekłego oraz sposobu jego aplikacji na etapach hermetyzacji i finalnego pokrywania jest niełatwy ze względu na rygorystyczne wymagania wobec produktu finalnego. Złożoność tego zagadnienia zwykle jest niedowartościowana na etapie projektowania.
Współpraca z producentem sprzętu do dozowania I pokrywania na etapie projektu pomaga w ustanowieniu efektywnego, skutecznego procesu. W niektórych konstrukcjach, wybrane elementy muszą być montowane ręcznie w wyżłobieniach obudowy i przymocowane śrubami, aby następnie utworzyć obudowę puszki połączeniowej. Zamiast tego, celem redukcji kosztów produkcji i jej automatyzacji, można zastosować płynną uszczelkę dozowaną automatycznie w bruzdach obudowy.
Aby sprostać wymaganiom dotyczącym niezawodności, spójności i powtarzalności aplikacji, niezbędne jest zastosowanie precyzyjnie sterowanych rozwiązań. Tradycyjne rozwiązania mogą szybko spotkać się z ograniczeniami. Jedynie poprzez zgodne połączenie platformy sprzętowej, oprogramowania oraz zaworu dozującego można osiągnąć niezawodny proces produkcyjny.
Pewność procesu
W celu zachowania stabilności procesów dozowania czy pokrywanie w dłuższym okresie czasu, a także osiągnięcia wysokiego stopnia traceability, niezbędne jest zastosowanie inteligentnych systemów, zdolnych ciągłego zbierania danych i automatycznej reakcji na zmiany. Wiele systemów kontroluje pozycjonowanie opierając się na zamkniętych systemach pomiarowych, co nie zawsze jest dostatecznie dobrym rozwiązaniem w przypadku procesu dozowania. Ze względu na zmiany właściwości materiałów, takich jak elastyczność, lepkość czy charakterystyka przepływu, zachowanie stabilności procesu jest często bardzo trudne w dłuższym okresie czasu.
Zmiany lepkości, powodowane przez upływ czasu, temperaturę czy wilgotność, moga mieć wpływ na klasyczne procedury dozowania, zmieniają one bowiem parametry przepływu, a co za tym idzie objętość oraz kształt dozowanego płynu. Wydaje się być oczywistym, iż bez dodatkowej regulacji, bezpieczne i powtarzalne dozowanie nie może być zapewnione.
Stosując procesy bezkontaktowego jetting’u oraz pokrywania, można stosować rozmaite ciecze na rozmaitych etapach procesu wytwarzania ogniw fotowoltaicznych. Przy zastosowaniu zaworów jet, dozowany płyn wtłaczany jest do zaworu pod niskim ciśnieniem. Niskie ciśnienie stosowane jest wyłącznie do celu wypełnienia zaworu, nie jest natomiast używane do pomiaru niezbędnej ilości płynu. Specjalnie opracowane usadowienie kulki stanowi mechanizm zamykający, w którym uniesienie kulki umożliwia wprowadzenia płynu do zaworu, ale nie wypłynięcie przez dyszę.
Za odmierzenie odpowiedniej porcji dozowanego płynu odpowiedzialny jest etap zamykania przepustu kulką: opadająca kulka wypycha płyn dalej, wtryskując go na substrat. Ten sposób przeprowadzenia operacji znacząco poprawia powtarzalność. W zależności od aplikacji, można wybrać mniejszą lub większą odległość pomiędzy dyszą a substratem. Głównymi zaletami jetting’u są większa szybkość oraz brak kontaktu z substratem. W rzeczywistości, czas pomiędzy dwiema dawkami wynosi około sześciu milisekund.
Dzięki opisanym rozwiązaniom, możliwe jest uzyskanie znacznie lepszych wyników dozowania. Rozpoznanie i stałe monitorowanie faktycznie przepływającej ilości cieczy stanowi znaczne wsparcie dla zapewnienia stabilnego procesu w dłuższym okresie czasu. Opatentowany system dozowania stosuje automatyczne rozwiązania dla programów jetting’u, dostarczając informacji, ważnych z punktu widzenia gromadzenia i przetwarzania danych.
Dawki są sprawdzane automatycznie, pomiar jest dokonywany w celu sprawdzenia czy sprawdzany parametr mieści się w granicach tolerancji. Wszystkie mierzone wartości są automatycznie zapisywane z datą i czasem pomiaru w pliku log, mamy, więc zapewnione śledzenie i monitorowanie parametrów procesu przez cały czas. Kiedy odchyłka parametru od zadanej wartości zostanie wykryta, kompensacja zostanie wykonana automatycznie by zapewnić stabilność procesu i jego przebieg w zadanych tolerancjach. Jeżeli pomiar wykryje, że zostały przekroczone tolerancję, zostanie wygenerowana wiadomość z kodem błędu i dalsza produkcja zostanie wstrzymana by uniknąć produkowania braków.