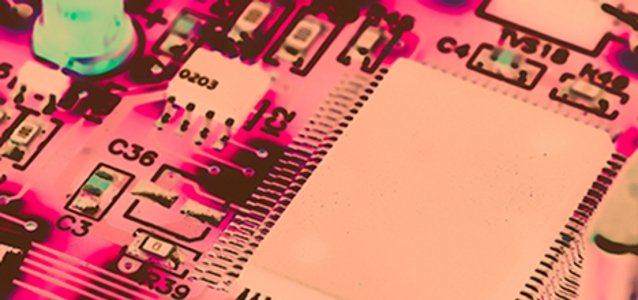
© anthony bolan dreamstime.com
Analizy |
Lutowanie w próżni przy produkcji komponentów MID
Artykuł prezentuje zalety lutowania z zastosowaniem próżni w procesie produkcji trójwymiarowych obiektów MID (molded interconnect device).
Zastosowanie technologii MID
Technologia MID ma w szczególności zastosowanie w tych aplikacjach, gdzie konieczna jest nie tylko miniaturyzacja i redukcja ilości elementów, ale również gdzie konieczny jest duży stopień ‘wolności’ wielowymiarowego projektowania. Elektryczne i mechaniczne funkcje, normalnie przypisane do kilku różnych składowych urządzenia, w technologii MID stanowią jedną, zespoloną część.
Przykładem jest inteligentny, samowystarczalny energetycznie czujnik ciśnienia, którego korpus wykonano właśnie w technologii MID. Jego konstrukcję, przeznaczoną do zastosowań w przemyśle motoryzacyjnym, wykonano w ramach wspólnego projektu realizowanego na zlecenie niemieckiego federalnego Ministerstwa Nauki i Badań. Rysunek 1, począwszy od lewej strony, przedstawia kolejne etapy procesu jego produkcji w technologii LPKF-LDS. Dzięki technologii MID czujnik może przybrać bardzo niewielkie rozmiary i składać się z ograniczonej ilości komponentów.
Rysunek 1: Korpus MID wykonany w technologii LPKF-LDS (strona lewa) oraz pionowo ułożone poszczególne poziomy montażu czujnika ciśnienia (strona prawa). Źródło: niemieckie federalne Ministerstwo Nauki i Badań
Wyzwania lutowania części 3D MID
Jak pokazano to na prawej części Rysunku 1, ze względu na trójwymiarowy projekt korpusu urządzenia, punkty styku pomiędzy korpusem oraz PCB rozmieszczone są pionowo. Rysunek 2 obrazuje ponadto, w jak niekorzystnej pozycji – dosłownie niczym ‘kubek’ - urządzenie musi być poddane lutowaniu kondensacyjnemu. W konwencjonalnym systemie lutowania vapor phase, tak niekorzystne położenie lutowanego elementu prowadzi do zbyt intensywnego nagromadzenia oparów. Prowadzi to w efekcie do niekorzystnych zjawisk: niektóre z połączeń lutowniczych są ogrzewane szybciej niż inne, znaczne są także straty medium w efekcie wyprowadzania z systemu części osadzonej w ‘kubku’.
Negatywne efekty nietypowego kształtu lutowanego elementu zostały zbadane w próbie, której pierwsza część polegała na lutowaniu kondensacyjnym w standardowym procesie z zastosowaniem próżni, ale bez etapu pre-vacuum, oraz przy zastosowaniu profilu odpowiedniego dla spoiwa bezołowiowego.
Wyniki testu lutowania kondensacyjnego bez etapu pre-vacuum
Rysunek 2 ukazuje w swojej lewej części rozmieszczenie pięciu termopar do poszczególnych poziomów montażowych utworzonych w korpusie MID oraz do jego górnej i dolnej krawędzi. Profile temperaturowe zostały zmierzone od etapu wprowadzania oparów Galdenu w warunkach atmosferycznych oraz przez całą pozostałą część procesu, w tym również po wprowadzeniu warunków próżni.
Linie profili w prawej części Rysunku 2 pokazują jasno znaczne różnice czasu nagrzewania się poszczególnych komponentów. Istotne różnice czasu transferu ciepła na komponent mają dwie pierwotne przyczyny. Po pierwsze, opary wznoszące się z dołu do góry już powodują pewne różnice czasu w dotarciu ciepła do dolnych oraz górnych partii urządzenia. Po drugie, powietrze, znajdujące się z dolnej części korpusu ukształtowanego w formie kubeczka, nie jest w pełni wypierane przez opary Galdenu. Oba te czynniki zakłócają przyrost temperatury w czasie oraz wpływają na proces przyjmowania ciepła przez poszczególne komponenty.
Rysunek 2: Rozmieszczenie termopar na korpusie urządzenia (strona lewa) oraz profile temperaturowe bez zastosowanie etapu pre-vacuum.
Wyniki testu lutowania kondensacyjnego z etapem pre-vacuum
W kolejnym kroku testu, przeprowadzonym przy identycznym rozkładzie termopar oraz ułożeniu komponentów, dodano również etap pre-vacuum. Polegał on na wytworzeniu od samego rozpoczęcia procesu próżni 100 mbar oraz wprowadzenia oparów Galdenu bezpośrednio do próżni. Rezultaty pomiarów zaprezentowane na Rysunku 3, wskazują jasno, iż wzrost temperatury w rozmaitych częściach urządzenia był zdecydowanie bardziej jednolity, co w efekcie umożliwiło bardziej ujednolicony proces przejścia ponad punkt topnienia we wszystkich obszarach lutowanego urządzenia.
Rozprzestrzenianie się oparów Galdenu w komorze procesowej
W warunkach próżni, opary Galdenu są rozprzestrzeniane w komorze procesowej równomiernie, podczas gdy w warunkach standardowych tworzą skłaniający się w dół obłok oparów, obserwowany na etapach podgrzania wstępnego oraz lutowania. W ten sposób można uniknąć zasadniczych wad zarówno procesu lutowania kondensacyjnego (im bliżej źródła ciepła tym elementy szybciej są nagrzewane) jak i lutowania konwekcyjnego (ponownie: im bliżej źródła ciepła tym elementy są nagrzewane szybciej, ale też dodatkowo osiągają wyższą temperaturę). Dzieje się tak ze względu na fakt, iż nie występuje w tym przypadku potrzeba usunięcia zbędnych mas powietrza, co oznacza błyskawiczne rozprzestrzenianie się molekuł gazu w opróżnionym obszarze. Czynnik ten na pozytywny wpływ na profil procesu lutowania oraz homogeniczność rozkładu temperatury na etapie ogrzewania, co w efekcie oznacza lepsza jakość lutowania.
Rysunek 3: Profile temperaturowe dla poszczególnych termopar z zastosowaniem etapu pre-vacuum.
Podsumowanie
Poprzez łączne zastosowanie lutowania kondensacyjnego oraz próżni, zniekształcenia spowodowane geometrycznym kształtem urządzenia są niwelowane. Dodatkowo, redukcji ulega liczba i rozległość pustek. Przy pomocy pomiarów profilu temperaturowego na różnych elementach korpusu MID udowodniono, iż możliwe jest wyraźne wyrównanie wzrostu temperatury na różnych obszarach lutowanego urządzenia po zastosowaniu etapu pre-vacuum. Utrzymały się ponadto niewielkie różnice temperatury szczytowej w poszczególnych obszarach urządzenia, co jest charakterystyczne dla lutowania kondensacyjnego.
Co więcej, etap pre-vacuum może byś stosowany w celu uzyskania szybszego i bardziej jednolitego podgrzewania komponentów o znacznej masie termicznej. Podsumowując można stwierdzić, iż zastosowanie próżni w procesie lutowania kondensacyjnego pozwala na wprowadzenie kolejnego, elastycznego czynnika, pozwalającego na uzyskiwanie idealnych profilów procesu lutowania, jak również zapobiega utracie części płynu galdenowego w przypadku lutowania elementów o kształcie zbliżonym do kubka.
Artykuł opracowany przez Helmuta Öttl, Head of Application and Prod[u][/u]uct Management, Rehm Thermal Systems
Artykuł opracowany i opublikowany dzięki uprzejmości firmy Scanditron.
© REHM
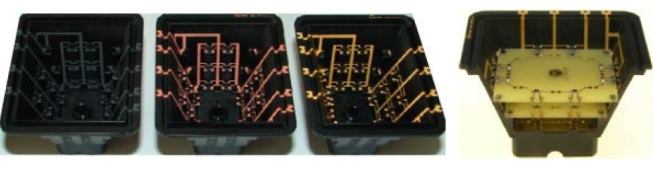
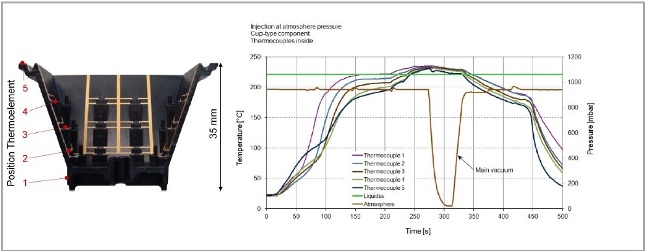
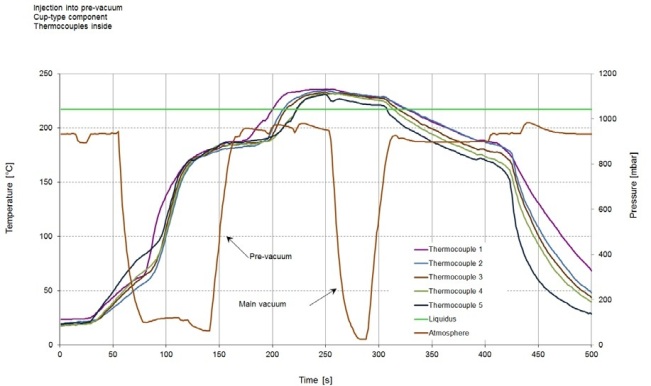