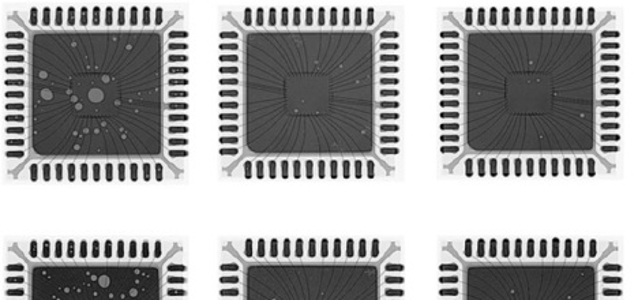
© REHM
Analizy |
Zalety lutowania w próżni: część 2
Druga część artykułu technicznego z poprzedniego tygodnia, prezentująca interesujący eksperyment badający wpływ lutowania w próżni na jakość lutowania komponentów z dolnymi wyprowadzeniami.
Po wprowadzeniu wybranych zagadnień związanych z wyzwaniami procesu lutowania komponentów BTC, w drugiej części artykułu omówiono wyniki testu lutowania przeprowadzonego w atmosferze próżni.
Rysunek 1: Topografia płytki testowej z pięcioma wzorami apertur dla komponentów BTC.
Rysunek 1 przedstawia generalny układ płytki testowej, z różnymi rodzajami komponentów. W dalszej części testu wzięto pod uwagę jedynie wyniki lutowania komponentów z wyprowadzeniami dolnymi.
Jak przedstawiono na rysunku 1, płytka zawiera po dwie identyczne apertury. Do nadruku wykorzystano dwa różne szablony, różniące się grubością i technologią wykonania. Pierwszy z szablonów to standardowy szablon o grubości 120 μm, bez żadnych specjalnych wykończeń. Drugi to szablon o grubości 110 μm, wykończony za pomocą technologii plazmowej i poddany procesowi elektropolerowania.
Płytkę poddano procesowi lutowania dwukrotnie, przy dwóch różnych profilach, z zastosowaniem próżni i bez, co opisuje Rysunek 2. W trakcie testu stosowano również etap tzw. ‘pre-vacuum’ w fazie podgrzewania wstępnego, co stabilizuje procedury testowe: testy lutowania przeprowadzane były przez cały dzień, co mogło wpływać przykładowo na stopień absorpcji wilgoci uwalnianej z topnika czy pasty i zniekształciłoby wyniki testu. Redukcja ciśnienia wpływa pozytywnie na stabilizację warunków, obniża bowiem punkt wrzenia płynów i ułatwia ich łagodniejsze wyparowywanie.
Należy zauważyć, iż zastosowanie próżni wydłużyło fazę pozostawania temperatury powyżej punktu topnienia lutowia o 30 sekund (porównaj: Rysunek 2). Proces redukcji pustek przy zastosowaniu próżni musi być kontynuowany przez cały czas pozostawania spoiwa w fazie płynnej I nie może równocześnie przebiegać zbyt szybko. W finalnej fazie płytkę poddano ciśnieniu 10 mbar przez 10 sekund.
Rysunek 2: Profil standardowy oraz profil z zastosowaniem próżni 10 mbar przez 10 sekund.
Porównanie wyników lutowania otrzymanych przy zastosowaniu opisanych dwóch profili przedstawiono na Rysunku 3. Można zaobserwować na nim drobne zmiany wyników w zależności od układu apertury, jednak należy stwierdzić, iż nie są one zbyt istotne. Znaczne natomiast różnice zaobserwowano przy zastosowaniu ciśnienia 10 mbar, przy którym obszar pustek na wszystkich połączeniach został zredukowany poniżej poziomu 2%.
Rysunek 3: Porównanie wyników lutowania z zastosowaniem próżni i w profilu standardowym.
Rysunek 4 ilustruje wyniki testu, powtórzonego przy zastosowaniu ciśnienia 100 mbar, zamiast 10 mbar jak w poprzedniej próbie. Również i w tym przypadku, liczba pustek została znacznie zredukowana, do poziomu < 3%.
Rysunek 4: Wyniki testu z zastosowaniem różnych poziomów próżni.
Można też stwierdzić, iż wybór geometrii apertury oraz wybór szablonu wydaje sie mieć znacznie mniejsze znaczenie niż zastosowanie próżni. Można jedynie odnieść wrażenie, iż zastosowanie szablonu wykończonego powłoką plazmową pomaga w uzyskaniu nieco lepszego rezultatu (skrajna prawa kolumna). Przyczyną tego zjawiska może być poprawione oddzielanie wilgotnej pasty od szablonu i związana z tym lepsza jej stabilność w przestrzeni.
Podsumowanie
Lutowanie z zastosowaniem próżni przyczynia się do znacznej redukcji zarówno ilości jak i powierzchni pustek. Celem zapobiegania uszkodzeniom wrażliwych komponentów oraz rozbryzgom pasty, system musi umożliwiać płynne profilowanie parametrów próżni, podobnie jak się to ma w przypadku profilowania temperatury.
Zastosowanie różnych geometrii apertur, jak również różnych typów szablonów, wydaje się nie mieć istotnego wpływu na powstawanie pustek podczas lutowania w otoczeniu próżni. W szerszym ujęciu, podzielenie dużych padów na mniejsze obszary może mieć pozytywny wpływ na charakterystyki nadruku wilgotnej pasty oraz jej stabilność, co prowadzi w konsekwencji do lepszych wyników montażu.
Trudno ponadto wskazać konkretny, zalecany poziom ciśnienia, jako że otrzymano pozytywne rezultaty przy różnym poziomie próżni. W zależności od grubości warstwy wilgotnej pasty, konkretnego jej rodzaju czy kształtu apertury, redukcja pustek do poziomu 2% może zostać uzyskana w szerokim zakresie od 10 do 100 mbar.
Artykuł opracowany przez Helmuta Öttl, Head of Application and Product Management, Rehm Thermal Systems
Artykuł opracowany i opublikowany dzięki uprzejmości firmy Scanditron.
© REHM
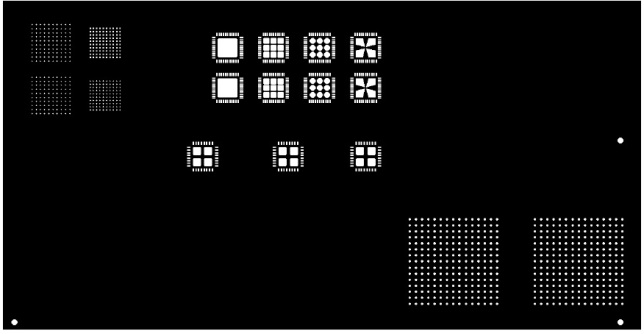
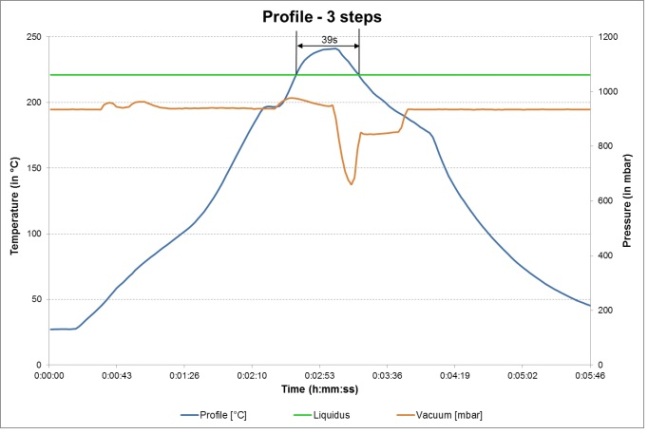
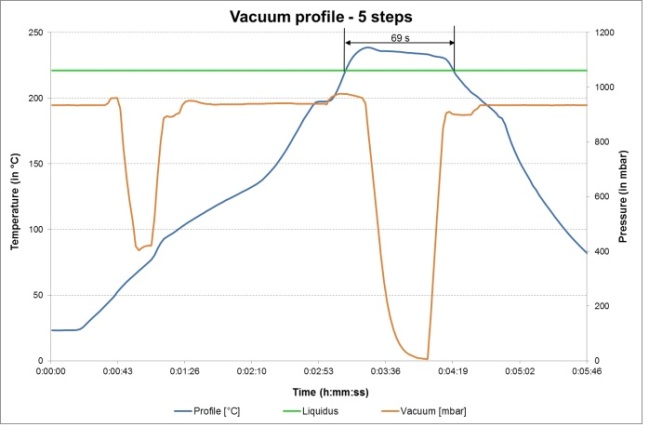
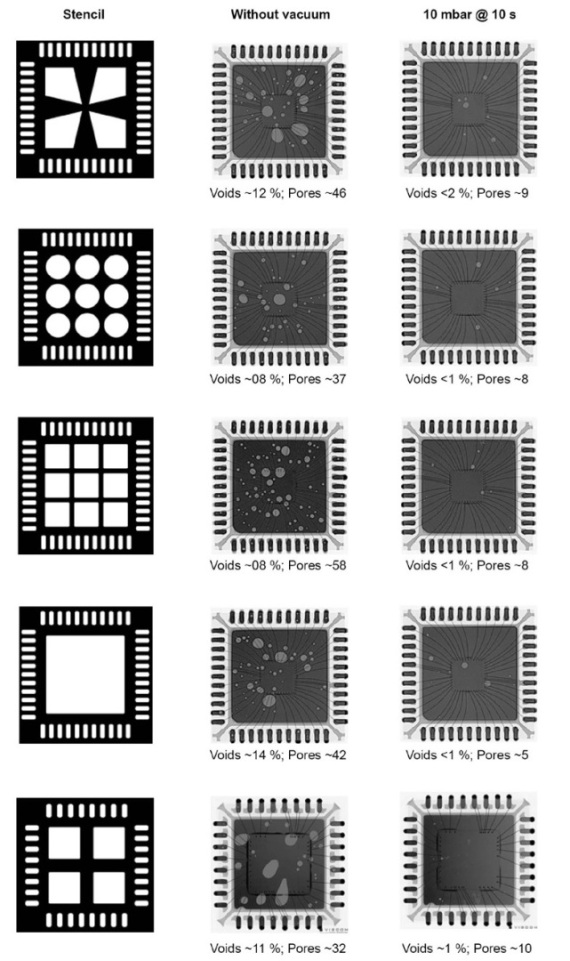
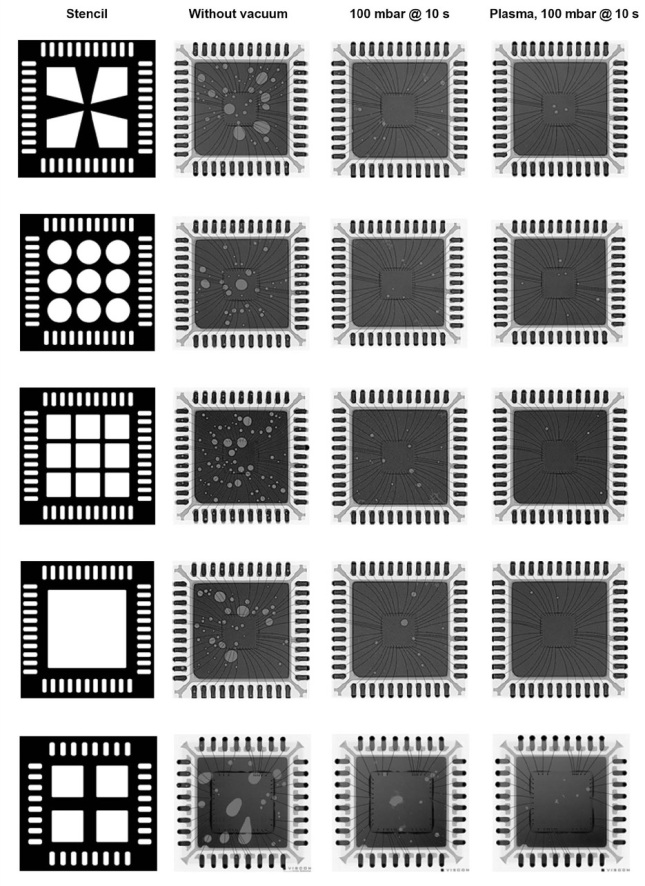