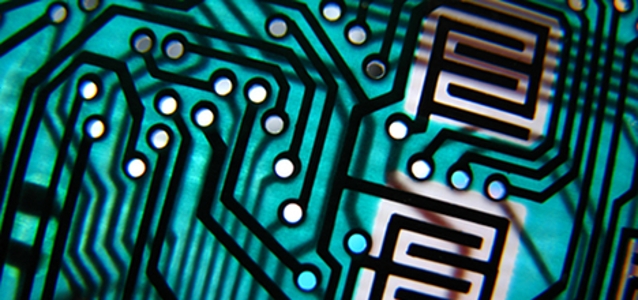
© photodynamx dreamstime.com
Analizy |
Technologia lutowania w oparach (część I).
W pierwszej części artykułu prezentującego technologię lutowania w oparach, przedstawiono nieco historii oraz materiały i urządzenia stosowane obecnie w procesie.
Wstęp
W początkowej fazie rozwoju technologii montażu powierzchniowego, lutowanie w oparach było preferowaną metodą montażu elementów elektronicznych, ponieważ gwarantowało doskonały transfer ciepła. Były jednak pewne wady związane z tą technologią, jak np. szybkie narastanie temperatury, brak wpływu na kształt profilu oraz wysokie koszty.
Dlatego zastosowanie technologii lutowania w oparach było ograniczone tylko do specjalnych aplikacji, obwodów drukowanych z dużymi obszarami masy, produkcji o niezbyt dużej wielkości (przykładowo w przemyśle zbrojeniowym, czy lotniczym).
Na przestrzeni ostatnich lat, technologia lutowania w oparach stale się rozwijała i udoskonalała. Dzisiaj oferuje nowe możliwości, przydatne zwłaszcza w technologii bezołowiowej. Główną zaletą najnowszych systemów lutowania w oparach jest niska temperatura procesu, możliwość sterowania gradientem temperatury w profilu temperaturowo-czasowym, automatycznie kontrolowany czas powyżej rozpływu, oraz atmosfera gazu obojętnego w trakcie lutowania.
Lutowanie od zawsze wiązało się ze stosunkowo wysokim podgrzaniem, takim by zapewnić odpowiednie warunki do rozpływu ciekłego lutowia. Dotyczy to wszystkich elementów na PCB, zarówno elementów biernych, aktywnych, jak i złącz oraz bardziej zaawansowanych układów typu BGA lub flipchip. Dlatego tak istotna jest kontrola temperatury procesu, aby zapobiec przegrzaniu elementów lub rozwarstwieniu laminatu. Zwłaszcza dla technologii lead-free okno procesu
robi się bardzo wąskie.
Lutowanie w oparach pozwala lutować obwody drukowane wykonane na laminacie FR4, z montażem dwustronnym, gęsto upakowanym. Proces jest niezawodny i całkowicie bezpieczny dla elementów lutowanych, dzięki wykluczeniu ryzyka przegrzania. Maksymalna temperatura procesu jest ograniczona do temperatury par medium w komorze procesowej i nie ma fizycznej możliwości jej przekroczenia. Urządzenia te pozwalają skutecznie przeprowadzić proces lutowania past ze stopami SAC już w temperaturze 230º.
Proces lutowania odbywa się w atmosferze gazu obojętnego, dlatego zwilżalność stopów lead-free w tej technologii jest prawie tak samo dobra jak tradycyjnych stopów SnPb. Najnowsze rozwiązania pozwoliły zastosować komorę próżniową w trakcie procesu lutowania w oparach, dzięki czemu uzyskuje się połączenia lutowane pozbawione pustek.
Zastosowanie komory próżniowej nabiera coraz większego znaczenia i znajduje coraz szersze zastosowanie szczególnie w elektronice "dużej mocy", gdzie istotne jest bardzo dobre lutowanie elementów do PCB.
Technologia lutowania w oparach, dzięki swoim zaletom, jak np. doskonały transfer ciepła, w połączeniu z nowymi urządzeniami i rozwiązaniami jest doskonałym narzędziem w procesie lutowania rozpływowego. Proces jest niezawodny, niezależnie od tego czy stosowane są stopy bezołowiowe czy tradycyjne SnPb.
1.Historia lutowania w oparach
1.1 Urządzenia
Proces lutowania w parach został opracowany w 1974r. przez dr. Phahl w Western Electric. Technologia ta znalazła szerokie zastosowanie w przemyśle we wczesnych latach 80-tych. Lutowanie rozpływowe w tym procesie umożliwiało prosty sposób transferu energii cieplnej na początkowym etapie rozwoju montażu powierzchniowego.
Lutowanie obwodów drukowanych z montażem SMT, było bardzo wygodne, bo tylko ta technologia gwarantowała możliwość wydajnego podgrzewania elementów. W początkowej fazie rozwoju technologii, piece do lutowania w parach charakteryzowały się dość dużą wielkością, były stosunkowo długie i ciężkie. Obwody drukowane w trakcie procesu przechodziły przez różne poziomy grzewcze ze stałą prędkością. Piece konsumowały duże ilości medium, które dodatkowo było krytyczne dla środowiska. Przemysł pracował nad alternatywnymi rozwiązaniami, piecami podczerwieni oraz konwekcyjnymi. Technologia lutowania w oparach była stosowana tylko w ograniczonym zakresie, w bardzo trudnych do lutowania przypadkach, o bardzo dużych obszarach masy z elementami wrażliwymi na przegrzanie.
Proces lutowania w parach był w efekcie rozwijany tylko przez kilku inżynierów, których działania skoncentrowały się nad opracowywaniem nowych technik, urządzeń oraz nowego typu medium.
1.2 Temperatura
Aby uzyskać połączenie lutowane o dobrej jakości, piece do lutowania w parach zapewniają temperaturę minimalnie powyżej temperatury topnienia stopu zastosowanego w paście lutowniczej użytej w produkcji. Pasty ze stopem ołowiowym były w przeszłości standardem w prawie wszystkich gałęziach przemysłu elektronicznego. Stop ten był eutektyczny i charakteryzował się temperaturą topnienia 183ºC.
Przez wiele lat zdobywano doświadczenie w pracy z tym stopem, dzięki czemu materiały stosowane do produkcji PCB i elementów elektronicznych oraz urządzenia produkcyjne spełniały bardzo dobrze wymagania procesu lutowania. Okno procesu było wystarczająco szerokie, aby zapewnić zadowalające warunki lutowania połączeń, z akceptowalnym poziomem narażeń termicznych elementów.
W procesie lutowania w parach z wykorzystaniem stopów ołowiowych, stosowane jest medium o temperaturze wrzenia 200ºC, dzięki czemu ryzyko narażenia elementów elektronicznych na szok termiczny jest zdecydowanie mniejsze niż w przypadku pieców konwekcyjnych.
Rysunek 1: Temperatura lutowania w oparach w technologii ołowiowej.
Standardowy proces lutowania stał się bardziej krytyczny w momencie, gdy wprowadzono w życie dyrektywę RoHS, która zabraniała stosowania ołowiu i innych niebezpiecznych materiałów w procesie montażu elektronicznego. Przemysł został zmuszony wprowadzenia zmian w technologii lutowania. Zmiany dotyczyły przede wszystkim stosowania nowych stopów lutowniczych, które charakteryzowały się wyższą temperaturą topnienia.
Wiele z tych nowych stopów zostało opatentowanych, przez co nie można mówić o jednym standardowym rozwiązaniu. Dzisiaj są stosowane różnych stopy lutownicze, z różną temperaturą topnienia. Najbardziej popularnymi stopami są dzisiaj te z rodziny SnAgCu, między innymi SAC305. Temperatura topnienia tego stopu zawiera się w przedziale 217ºC a 221ºC. W procesie lutowania w parach temperatura w peaku dla takiego stopu wynosi 230ºC.
Kolejnym szeroko stosowanym, przez wielu producentów, stopem jest tańszy stop SnCu z temperaturą topnienia 227ºC. W technologii lutowania w parach, stosujemy w tym wypadku medium o temperaturze wrzenia 240ºC. Z uwagi na wymagania niektórych producentów dotyczących maksymalnej temperatury procesu lutowania ograniczonej do 235ºC został opracowany płyn, który posiada właśnie taką temperaturę wrzenia. Oczywiście płyn ten umożliwia lutowanie w parach również stopów bezołowiowych o niższych temperaturach procesu: od 217ºC do 227ºC.
Rysunek 2: Temperatura lutowania w oparach w technologii bezołowiowej.
W technologii lutowania w oparach temperaturę procesu została ograniczone przez fizyczne właściwości stosowanego medium, dlatego ryzyko przegrzania elementów lutowanych zostało zminimalizowane. Gęstość par medium jest dużo większa niż gęstość otaczającego powietrza, dlatego elementy lutowane w trakcie całego procesu znajdują się w atmosferze obojętnej i są zwilżane przez lutowie w tym samym czasie. Powietrze powyżej par medium jest chłodzone do poziomu 50ºC - 80ºC.
2. Lutowanie w oparach dzisiaj
2.1 Materiały
Wprowadzenie nowych stopów lutowniczych, charakteryzujących się wyższą temperaturą topnienia, jest jednym z poważniejszych wyzwań w lutowaniu bezołowiowym. Pasty do lutowania rozpływowego, zawierające stopy lead-free, w trakcie lutowania wykazują gorszą zwilżalność i mogą wymagać obojętnej atmosfery procesu.
Dlatego w przypadku pieców konwekcyjnych stosowany jest tunel azotowy, aby poprawić zwilżalność i ochronić kontakty elementów elektronicznych przed utlenianiem w podwyższonej temperaturze. W technologii lutowania w parach, proces z zasady swojego przebiegu zapewnia atmosferę obojętną, dlatego nie są potrzebne dodatkowe źródła gazu ochronnego.
Podłoża stosowane w produkcji PCB nie uległy specjalnej zmianie. Szklano - epoxydowy laminat FR4 nadal jest podstawowym materiałem zarówno dla projektów jedno- jak i wielowarstwowych. Podłoża te są wrażliwe na podwyższoną temperaturę i mają tendencję do delaminacji. W przemyśle elektronicznym zjawisko delaminacji podłoży jest trudne do detekcji za pomocą standardowych urządzeń detekcyjnych. Co więcej, moduł elektroniczny z tego typu uszkodzeniem może pracować poprawnie, w krótkim okresie po produkcji, ale pod wpływem wibracji i zmian temperatury uszkodzenie będzie się pogłębiało.
W przypadku innych materiałów plastycznych stosowanych w obudowach elementów elektronicznych, oraz w różnych podłożach mamy również do czynienia z problemami związanymi z wrażliwością na podwyższoną temperaturę. Materiały te także nie uległy znaczącym zmianom w trakcie przejścia na technologię lead-free.
Elementy elektroniczne z jednej strony są coraz bardziej zaawansowane, a z drugiej coraz mniejsze. Wymagają zatem coraz większej precyzji w procesie montażu elektronicznego, dotyczy to zarówno procesu drukowania pasty lutowniczej jak i układania. Dodatkowo im mniejszy jest element tym droższa jest kontrola jakości jego montażu. Jakość lutowania układów w obudowach BGA nie może być sprawdzona bez drogich urządzeń inspekcyjnych opartych na promieniowaniu rentgena. Jeśli takie zaawansowane układy nie są popranie lutowane w pierwszym procesie, ich ewentualna naprawa jest kosztowna i zajmuje wiele czasu.
Technologia LED wyparła tradycyjne żarówki oraz lampy fluoroscencyjne. Diody o małych rozmiarach, są bardzo wydajne jako źródło światła. Aby wydłużyć ich czas życia, projekty obwodów drukowanych muszą pozwalać na odbiór ciepła z grzejących się elementów. W efekcie połączenie elementów elektronicznych o bardzo małych rozmiarach, z obwodami drukowanymi posiadającymi duże obszary masy stanowi poważne wyzwanie dla tradycyjnego procesu lutowania w piecach konwekcyjnych.
W takich sytuacjach zalety technologii lutowania w parach nabierają znaczenia. Niska temperatura procesu, równomierny rozkład temperatury na PCB oraz bardzo dobra zwilżalność pozwalają sprostać najtrudniejszym wymaganiom.
Nowoczesne systemy lutowania w oparach produkowane są z wysokiej jakości stali i aluminium. Jest to szczególnie istotne, gdy elementy te są narażone na działanie wysokiej temperatury.
2.2 Medium
Nowoczesne płyny, które są podstawową technologii lutowania w oparach, oparte są na perfluoropolyeterach. Nie zawierają freonów, ani innych związków chemicznych niebezpiecznych dla zdrowia. Związki te są nietoksyczne, charakteryzują się brakiem przewodności elektrycznej, są niepalne i mają niską lepkość. Transport tych materiałów nie jest w żadnym stopniu niebezpieczny. Ich przechowywanie nie jest regulowane specjalnymi przepisami.
Najpowszechniej stosowane płyny, w technologii lutowania w oparach zostały wymienione poniżej (w nawiasie podano ich temperaturę wrzenia).
Lutowanie ołowiowe
LS 200 (200ºC)
LS 215 (215ºC)
Lutowanie bezołowiowe LS 230 (230ºC)
LS 240 (240ºC)
IBL 225 (225ºC)
IBL 235 (235ºC)
W sytuacjach, gdy nie jest znana precyzyjna informacja na temat stopu w kulkach BGA lub w innych ważnych elementach elektronicznych, nie mamy wiedzy o pokryciu obwodu drukowanego itp. zalecane jest stosowanie medium o temperaturze wrzenia 235ºC. Taki płyn jest kompromisowym rozwiązaniem dla wszystkich bezołowiowych aplikacji i gwarantuje najlepsze rezultaty.
2.3 Urządzenia
Na rynku jest obecnych kilku dostawców urządzeń do lutowania w parach. Oferują oni różne rozwiązania w szerokim zakresie typów urządzeń, od najmniejszych agregatów lutujących przeznaczonych do produkcji prototypowej, zastosowań laboratoryjnych, testów oraz reworku, po najbardziej zaawansowane urządzenia pracujące w trybie in-line.
W niektórych przypadkach wymagana jest bardzo wysoka jakość połączeń lutowanych, pozbawionych przede wszystkim pustek (voids). W takich sytuacjach rozwiązaniem jest proces lutowania w parach, przeprowadzany w komorze próżniowej.
Rysunek 3: Proces lutowania w oparach w próżni
Zastosowanie modułów IR w fazie podgrzewania może być pomocne w skróceniu czasu trwania procesu, ewentualnie może być wykorzystane do utwardzania kleju SMT. Piece do lutowania rozpływowego w parach charakteryzują się mniejszymi rozmiarami, dlatego potrzebują mniej miejsca w obszarze produkcji niż porównywalne piece konwekcyjne. Technologia ta charakteryzuje się również mniejszą energochłonnością niż tradycyjne piece reflow. Zużycie energii w procesie Vapour Phase jest kilkakrotnie mniejsze niż w przypadku konwekcji.
© C.H.Erbsloeh, IBL
Artykuł opracowała firma C.H.Ersbloeh. Część druga artykułu w najbliższy piątek.
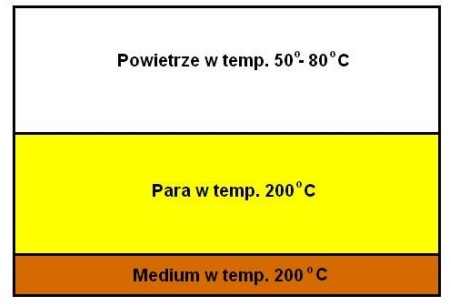
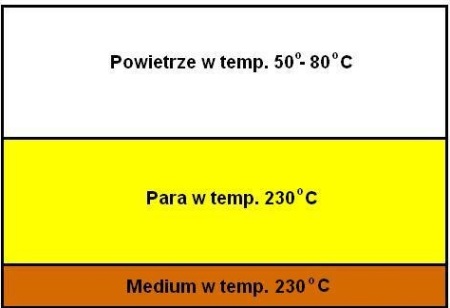
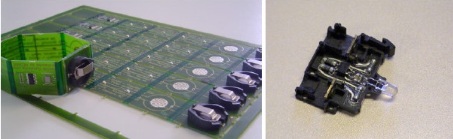
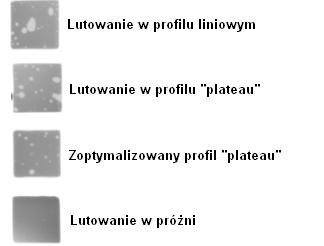