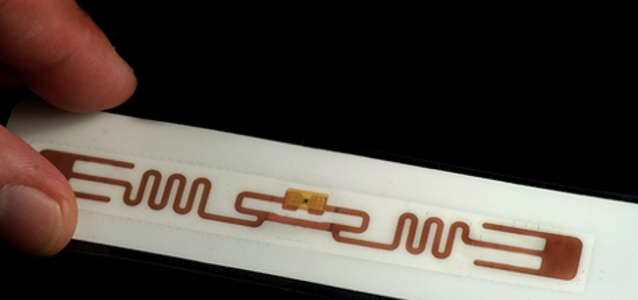
© albert lozano dreamstime.com
Przemysł elektroniczny |
Elektronika drukowana jak gazety
Naukowcy z ITR-u pracują nad drukowaniem modułów elektronicznych na takich materiałach jak ludzka skóra czy soczewka kontaktowa, wykorzystując do tego tanią technikę druku.
Projekt dotyczący elektroniki organicznej, drukowanej i elastycznej rozpoczął się w Instytucie Tele- i Radiotechnicznym w 2009 roku i jak na razie nie widać jego końca, bo wciąż pojawiają się nowe obszary do zbadania. Sześć lat temu technika druku elektroniki była jeszcze na etapie pomysłów; dzisiaj naukowcy z ITR-u dysponują maszynami i tuszami do produkcji elektroniki drukowanej oraz pracują nad ich konkretnymi zastosowaniami.
Ale wróćmy jeszcze na chwilę do 2009 roku, gdy Komisja Europejska przedstawiła mapę drogową rozwoju elektroniki organicznej, zwanej dzisiaj częściej drukowaną. Materiały używane w tej technice produkcji to związki organiczne lub materiały na bazie związków organicznych. Mają tę zaletę, że da się je wytwarzać w formie roztworów, które z kolei można doprowadzić postaci farb i tuszy stosowanych w procesie poligraficznym. – Umożliwiło to wykorzystanie wielkoseryjnych technik poligraficznych do wytwarzania elektroniki, co z kolei otworzyło zupełnie nowe obszary zastosowań elektroniki, o których nie można było do tej pory nawet myśleć – mówi Konrad Futera z Instytutu Tele- i Radiotechnicznego, doktorant Wydziału Mechatroniki Politechniki Warszawskiej.
Korzystając z urządzeń opracowanych w Instytucie da się wytworzyć element elektroniczny na wszystkim, z czym miała do czynienia poligrafia: na papierze, folii szklanej, polimerowej, na skórze wyprawionej lub żywej, a także na materiałach bardzo delikatnych, takich jak soczewki kontaktowe. – Stosowana przez nas technika druku strumieniowego ma tę zaletę, że jest bezstykowa. Dzięki temu możemy drukować nawet na cieczach lub żelach. Możliwe zastosowania to elementy wykonane na podłożach z ceramiki nieutwardzonej. Do tej pory w tym celu wykorzystywano sitodruk, przez co podłoże deformowało się w procesie produkcji – opowiada Konrad Futera.Chociaż elektronika drukowana nigdy nie będzie mogła bezpośrednio konkurować z elektroniką krzemową pod względem wydajności, to ma kilka zasadniczych atutów, których brakuje układom scalonym wykonanym tradycyjnymi technikami. – Po pierwsze elektronikę drukowaną nanosimy na materiały miękkie, elastyczne i niekoniecznie płaskie. Wykorzystując technikę druku strumieniowego możemy drukować na elementach o skomplikowanym kształcie – wyjaśnia Konrad Futera. Jednym z możliwych zastosowań jest antena telefonu komórkowego nadrukowana bezpośrednio na obudowie. Takie rozwiązanie oszczędza miejsce na płytce drukowanej, zapewnia świetną izolację układów antenowych od reszty modułów, a co więcej, jest tanie. – Dzięki wykorzystaniu technik drukarskich koszt wytworzenia pojedynczego elementu jest liczony w dziesiątych częściach centa – ocenia Konrad Futera. A ile kosztuje maszyna skonstruowana przez zespół z ITR-u? Zacznijmy od tego, że analogiczne maszyny poligraficzne to koszt średnio 200 tys. EUR. Tymczasem pierwsza wersja sprzętu opracowanego w Instytucie kosztowała 100 tys. PLN, a po poprawkach i usprawnieniach, koszt zamknie się w 50 tys. PLN. Oczywiście tradycyjne maszyny poligraficzne nie nadają się do drukowania komponentów elektronicznych. - Trzeba było opracować urządzenie odpowiednie do prac z tuszami stosowanymi przy wytwarzaniu elektroniki. Ale największy minus urządzeń poligraficznych, to brak ciągłej kontroli procesu. Jeden wydruk zajmuje czasem nawet kilkanaście godzin i przeprowadza się go w wielu etapach. Gdyby na jakimkolwiek etapie wystąpił błąd, cała nasza praca poszłaby na marne, dlatego wyposażyliśmy maszynę w elementy ciągłej kontroli procesu, takie jak zestaw czujników, kamer i odpowiednie oprogramowanie – wyjaśnia Konrad Futera. – Kontrolujemy każdą kroplę tuszu od chwili wystrzelenia z głowicy, obserwujemy jej lot, moment, gdy uderza w podłoże, proces wchłaniania i możemy w odpowiednim momencie zareagować na ewentualne problemy – opisuje naukowiec, podkreślając, że jest to kluczowa sprawa przy produkcji elektroniki drukowanej. Warto przy tym wspomnieć, że do wytworzenia elementu diody elektroluminescencyjnej, czyli już dość skomplikowanego układu, potrzeba około 4-5 tys. kropel. Natomiast jedna kropla to zaledwie 4 pikolitry tuszu. Również w Instytucie powstają specjalne tusze do druku elektroniki. – Optymalizujemy i komponujemy tusze oparte o nanocząstki srebra, które w tej chwili są w powszechnym użyciu i które mają świetne właściwości przewodzące. Pracujemy także z tuszami zawierającymi płatki grafenowe i jesteśmy na etapie zakończenia wdrażania maszyny drukującej przy użyciu tuszy heterofazowych na płatkach grafenowych przy współpracy z Instytutem Technologii Materiałów Elektronicznych ITME oraz z prof. Małgorzatą Jakubowską z PW. Dzięki temu urządzeniu uda się opracować technikę produkcji transparentnych elementów elektronicznych opartych na tuszach grafenowych – mówi Konrad Futera. Projekt wciąż jest rozwojowy, widać zainteresowanie firm high-tech, często tych, które działają w branży kosmicznej, lotniczej czy wojskowej. Naukowcy sporo uwagi poświęcają też grafenowi. – Prowadzimy prace nad tranzystorem grafenowym. Mamy duże nadzieje w tej sprawie, ale najpierw musimy dobrze opracować technikę nakładania tuszy opartych na grafenie, żeby mówić o wykorzystaniu jego właściwości półprzewodnikowych – mówi Konrad Futera. Jeśli naukowcom uda się osiągnąć swój cel, będą jednymi z pierwszych na świecie, którym uda się zastosować komercyjnie grafen. – Pracujemy nad wdrożeniem naszej techniki druku strumieniowego do nanoszenia warstw grafenowych. Jako jedni z pierwszych mamy pomysł, jak realnie zastosować materiały grafenowe w elektronice i osiągamy dobre wyniki – ocenia Konrad Futera.