Sponsored content by Milar
Ochrona elektroniki samochodowej powłokami ochronnymi – lakiery UV
Elektronika samochodowa, niegdyś słabo rozwinięty segment rynku, zyskała w ostatnich latach duże znaczenie, ponieważ zmieniła się branża, kultura i oczekiwania klientów. Wzrosły wymagania dotyczące bezpieczeństwa i przepisów dla pojazdów, producenci mają nowe wymagania gwarancyjne, a to, co kiedyś było „luksusem”, teraz powinno być standardem w nowym samochodzie.
Funkcje takie jak: utrzymywanie pasa ruchu, kamery skierowane do tyłu, zautomatyzowane parkowanie i inne rodzaje wspomaganej jazdy stają się powszechne, ponieważ cele producentów skierowane są w stronę samojezdnego (autonomicznego) samochodu. Pełne systemy informacyjno-rozrywkowe, obejmujące oprogramowanie do nawigacji, odtwarzania muzyki, komunikacji i szereg mniej typowych aplikacji, również zyskują na popularności.
Zasadniczo oczekuje się, że każdy nowy pojazd na rynku będzie bezpieczny, wygodny i niezawodny. Te cechy zależą w dużym stopniu od jakości zastosowanych komponentów elektronicznych. Sterowanie poduszkami powietrznymi, układy wtrysku paliwa, sterowanie zawieszeniem, automatyczne skrzynie biegów, moduły elektrycznie sterowanych szyb i drzwi, moduły sterujące silnikiem i układem klimatyzacji to niewielki ułamek obecnych układów elektronicznych spotykanych w przeciętnym nowym samochodzie. Użycie elektroniki jest jeszcze większe w pojazdach hybrydowych. Oprócz wzrostu zawartości elektronicznej na pojazd, nastąpił również wzrost ogólnej sprzedaży pojazdów, szczególnie w obu Amerykach i Azji (dane sprzed pandemii COVID-19).
Jakość i niezawodność elektroniki w samochodach wpływa na decyzje konsumentów. Producent pojazdów, który cieszy się opinią producenta elektroniki, która szybciej zawodzi, napotka więcej trudności na rynku i będzie miał więcej napraw gwarancyjnych.
Oznacza to, że istnieje potrzeba tworzenia nie tylko dobrze przetestowanego oprogramowania, ale także dobrze zmontowanego urządzenia. Samochód jest trudnym środowiskiem pracy dla płytki PCB, w zależności od umiejscowienia płytki, intensywności użytkowania pojazdu i rodzaju środowiska, na które jest narażony. Delikatne elementy elektroniczne i ścieżki między nimi muszą być chronione, aby działały niezawodnie.
Deskę można odsłonić, zaprojektować we własnej obudowie lub zalać odpowiednią żywicą. Zamknięcie lub zalewanie zajmuje miejsce i sztucznie ogranicza przestrzeń dostępną dla elektroniki. Zalewanie całych obwodów drukowanych również zwiększa wagę, jednak projektanci pojazdów są coraz bardziej zainteresowani usuwaniem z samochodu każdej niepotrzebnej uncji. Istnieje jednak alternatywne rozwiązanie.
Używanie powłok lakierniczych
Powłoki konformalne to polimery, które można nakładać cienkimi warstwami na płytki obwodów drukowanych, aby chronić i izolować elektrycznie komponenty przed obciążeniami środowiskowymi.
W zależności od potrzeb mogą być natryskiwane, nakładane pędzlem, powlekane przez polewanie lub dozowane przez roboty i zajmują bardzo mało dodatkowej przestrzeni. Typowa grubość wynosi od 0,002'' do 0,005'' z możliwością nakładania grubszych powłok w razie potrzeby. Powłoki konformalne pozwalają na mniejsze, lżejsze zespoły, ponieważ nie są potrzebne żadne dodatkowe obudowy, co umożliwia umieszczenie większej liczby płytek drukowanych w tej samej przestrzeni. Rys. 1. Przezroczysta powłoka ochronna
Ponadto ich zdolność do izolacji może poprawić wydajność i pozwolić na znaczne zmniejszenie potrzebnej przestrzeni między ścieżkami na płycie.
Pomimo cienkiej warstwy są bardzo skuteczne. Powłoki konformalne chronią płytki przed naprężeniami mechanicznymi i termicznymi, wilgocią, substancjami korozyjnymi, zanieczyszczeniami, takimi jak sól i brud, szkodliwymi gazami, grzybami i innymi czynnikami środowiskowymi, na które mogą napotkać PCB w pojazdach.
Wzrost wąsów cyny pojawia się z czasem na elementach PCB i jest stymulowany przez naprężenia mechaniczne i termiczne, które są szczególnie powszechne w zastosowaniach motoryzacyjnych. Powłoki ochronne mogą spowolnić ten wzrost, zapobiegając powstawaniu łuków i zwarć. Powłoki zwiększają również wytrzymałość mechaniczną komponentów i poprawiają trwałość zmęczeniową połączeń lutowanych.
W branży motoryzacyjnej płytki PCB są umieszczane tam, gdzie najlepiej pasują do danego układu pojazdu - czyli praktycznie w każdym miejscu samochodu. Czujniki i płytki drukowane znajdują się w miejscach, które mogą być narażone na wszystko, od płynu hamulcowego po opary benzyny, mgłę solną oraz wszelkie ciepło i wibracje związane z silnikiem spalinowym. Odpowiedni rodzaj powłoki ochronnej zapewni ochronę i nie doda dodatkowej nieefektywności do procesu produkcyjnego.
Zalety powłok światło-utwardzalnych
Dostępne są różne typy powłok ochronnych, w tym na bazie rozpuszczalników, silikonowe, dwuskładnikowe epoksydy i akrylany uretanowe. Powłoki światło-utwardzalne mają kilka zalet w porównaniu z innymi systemami.
Powłoki ochronne UV utwardzają się na żądanie w ciągu kilku sekund i są łatwiejsze do zautomatyzowania jako cały proces niż inne rodzaje powłok. Nie ma potrzeby układania w stosy i tymczasowego zabezpieczania płytek, a następnie poddawania ich dodatkowej obróbce. Oprócz oszczędności czasu, technologia światło-utwardzalna oszczędza również miejsce na hali produkcyjnej i zwiększa ogólną wydajność. Nie ma potrzeby mieszania, jak w przypadku dwuskładnikowych epoksydów, nie ma potrzeby zabezpieczania przeciwwybuchowego, jak w przypadku powłok na bazie rozpuszczalników, i zazwyczaj na każdym etapie przetwarzania wymagana jest mniejsza liczba kroków i mniej operatorów. Ponadto nie są wymagane żadne dodatkowe opłaty za wysyłkę, co może mieć miejsce w przypadku materiałów niebezpiecznych.
Materiały światło-utwardzalne mogą nie zawierać silikonu i rozpuszczalników.
Mechanizm utwardzania jest dość prosty. Kiedy światło wytwarzające energię o prawidłowej mocy widmowej zetknie się z materiałem światło-utwardzalnym (LCM), fotoinicjatory w materiale fragmentują się, tworząc wolne rodniki, rozpoczynając proces utwardzania. Wolne rodniki zaczynają tworzyć łańcuchy polimerowe z akrylanami, które stanowią LCM, aż wszystkie dostępne rodniki przyłączą się i staną się stałym polimerem. Następuje koniec procesu utwardzania zwany terminacją i LCM uległa polimeryzacji lub utwardzeniu.
Dobór odpowiedniej powłoki ochronnej
Środowisko końcowego użytkowania i testy kwalifikacyjne symulują środowisko, w którym PCB i powłoki ochronne będą ostatecznie używane przez cały okres eksploatacji pojazdu. Oczekiwane ekstremalne temperatury, wilgoć, ścieranie, rozpylona sól, wibracje, chemikalia i inne potencjalne lub prawdopodobne zagrożenia wpłyną na to, jakie konkretne powłoki ochronne są optymalne dla danego zastosowania. Konieczne jest również rozważenie wymaganych właściwości elektrycznych w celu zapewnienia integralności elektrycznej modułu.
Większość światło-utwardzalnych powłok z akrylanów uretanowych działa dobrze w temperaturach roboczych od -40 do 150° C, chociaż niektóre mogą być również stosowane w temperaturach poniżej -40° C. Powłoki te charakteryzują się dobrą odpornością chemiczną i na wilgoć.
Ogólnie rzecz biorąc, światło-utwardzalne powłoki o większej twardości (twardsze) mają zwykle wyższą odporność chemiczną i na ścieranie i są szczególnie korzystne, jeśli pożądane są cienkie warstwy pokrycia. Bardziej miękkie powłoki o niższej twardości zmniejszają naprężenia elementów i zapewniają najlepszą odporność na szoki termiczne. Aby uzyskać wyższą odporność chemiczną bardziej miękkich powłok, można zastosować nieco grubszą powłokę.
Testy niszczące będą przydatne do określenia, jaka powłoka i rodzaj aplikacji są najlepsze dla produkowanych obwodów drukowanych.
Rodzaje specjalistycznych powłok UV
Ten rodzaj powłoki został opracowany, aby zapewnić całkowite utwardzenie w zastosowaniach, w których problemem są zacienione obszary na płytkach drukowanych o dużej gęstości. Są zaprojektowane z mechanizmami utwardzania wtórnego lub termicznego. Nasze formuły utwardzania wilgocią zapewniają utwardzanie obszarów zacienionych w czasie za pomocą wilgoci, eliminując potrzebę drugiego etapu procesu i obawy o degradację żywotności komponentów w wyniku ekspozycji na temperaturę.
Rys. 2. Utwardzona powłoka w miejscu zacienionym
Jest to szczególnie skuteczne podczas klejenia tworzyw sztucznych, które naturalnie fluoryzują na niebiesko, takich jak PV i PET. Technologia Ultra-Red® tworzy również unikalną sygnaturę widmową, której mogą używać producenci do uwierzytelniania produktu.
Rys. 3. Jaskrawoczerwona fluoryzacja
Czarna powłoka ochronna została opracowana specjalnie w celu ochrony poufnych informacji na PCB. Podobnie jak typowa powłoka ochronna, poprawia niezawodność obwodu w trudnych warunkach, ale dzięki matowemu czarnemu kolorowi ma dodatkową zaletę w postaci możliwości ukrycia oznaczeń, etykiet, poufnych informacji i innych elementów identyfikacyjnych na płytce drukowanej. Ta powłoka ma doskonałe kryje i może być nakładana i utwardzana do 5 mili grubości w jednym przejściu. Można go również dozować w wielu przejściach, jeśli wymagana jest grubsza powłoka.Rys. 4. Matowe czarne pokrycie
Ta powłoka składa się w 100% z części stałych i ma lepkość zaledwie 20 cP, co czyni ją idealnym wyborem do powlekania błoną / polewaniem lub podobnych metod dozowania. Utwardza się pod wpływem UV / światła widzialnego, ale może być również utwardzany ciepłem do zastosowań w miejscach zacienionych. Powłoka jest zoptymalizowana pod kątem diod LED, utwardza się w ciągu zaledwie kilku sekund do natychmiastowej obróbki. Powłoka również fluoryzuje na niebiesko w czarnym świetle, umożliwiając łatwiejszą inspekcję pokrycia płytki.
Rys. 5. Pokrycie lakierem o niskiej lepkości
Metody nakładania/aplikacji
Istnieje kilka powszechnych metod nakładania powłok światło-utwardzalnych, w tym automatyczne nakładanie selektywne, natrysk ręczny, natrysk i pędzel.
Zanurzanie jest rzadko praktykowane w przypadku tego rodzaju powłok, ponieważ wymaga bardziej złożonej konfiguracji sprzętu ze względu na wrażliwość na światło. Co za tym idzie, trudniej jest odpowiednio kontrolować grubość powłoki, jak i jej jednolitość.
Zautomatyzowana aplikacja selektywna wykorzystuje robotykę do wielokrotnego i niezawodnego nakładania powłok w celu zminimalizowania czasu, strat materiałowych i kosztów pracy. W ten sposób można stosować techniki rozpylane (rozpylanie) lub nie rozpylane (szczotkowanie lub natryskiwanie). Procesy nie rozpylone i rozpylone mogą być również stosowane w tandemie, jeśli jest to potrzebne dla określonego rodzaju obwodu drukowanego. Pomyślne zastosowanie pokrycia selektywnego zależy od możliwości robota i topografii płytki.
Rys. 6. Nakładanie powłoki metodą natryskową.
Natrysk ręczny jest powszechną tanią metodą, ponieważ wiele płyt może być przetwarzanych w tym samym czasie przy minimalnym wymaganym koszcie kapitałowym. Jednak uzyskanie pożądanej grubości powłoki wymaga więcej pracy i staranności. Konieczne jest maskowanie obszarów chronionych, a aplikacja może wymagać wielu przejść powłoki z różnych kierunków, aby uzyskać jednolite pokrycie.
Powłokę można nakładać również za pomocą pędzla i ten rodzaj aplikacji częściej używany jest do poprawek lub małych obszarów. Niezawodność i powtarzalność w dużym stopniu zależą od operatorów.
Istotne jest, aby wybrać najlepszy system dozujący do danego zastosowania. Dostępnych jest wiele opcji, w zależności od tego, co działa najlepiej z wybraną powłoką ochronną, i należy zadbać o to, aby wszystkie części systemu były ze sobą kompatybilne. Dostępne jest specjalne żółte oświetlenie, które zapobiega przedwczesnemu utwardzaniu pod wpływem światła z otoczenia. Uważa się, że najlepiej jest, gdy wszystkie części systemu dozującego są całkowicie nieprzezroczyste.
Powlekanie płytki w celu jej ochrony jest mniej skuteczne, jeśli płyta jest zanieczyszczona i w rzeczywistości powłoka może uszczelniać istniejące zanieczyszczenia. Z biegiem czasu takie zanieczyszczenia mogą reagować nawet z niewielkimi ilościami wilgoci i prowadzić do rozwarstwienia w tym obszarze. Zanieczyszczenia te mogą również zapobiegać lepszemu przyleganiu powłoki do płyty. Dlatego ważne jest, aby upewnić się, że podłoże jest czyste przed nałożeniem jakiejkolwiek powłoki ochronnej, zazwyczaj przy użyciu rozpuszczalnika lub wody, a następnie zalecanego cyklu suszenia, i przechowywać w worku do wyładowań elektrostatycznych, jeśli konieczne jest przechowywanie.
Najlepszą praktyką jest obsługiwanie płytek w rękawiczkach, tak aby oleje, brudy lub inne zanieczyszczenia nie przedostały się z rąk ludzkich na PCB.
Jeśli z jakiegoś powodu płytki nie mogą być wyczyszczone, ważne jest, aby sprawdzić, czy spełnią wszystkie końcowe wymagania przy istniejącym poziomie zanieczyszczenia. Ulepszone światło-utwardzalne powłoki o lepszym zwilżaniu zostały zaprojektowane tak, aby ograniczyć wpływ zanieczyszczeń płytowych, takich jak topnik no-clean.
Wszystkie zatwierdzone w branży powłoki ochronne fluoryzują pod wpływem czarnego światła, co pomaga operatorom sprawdzić, czy powłoka została nałożona całkowicie i prawidłowo. Nowsze laserowe systemy pomiarowe 3D są teraz dostępne również do zastosowań wymagających wysokiej niezawodności.
Proces utwardzania
Aby uzyskać pełne i niezawodne utwardzenie materiałów światło-utwardzalnych, ważne jest, aby wybrać źródło światła o mocy widmowej, która odpowiada widmom absorpcji fotoinicjatorów w LCM, z optymalną intensywnością dla danego zastosowania.
Zwykle utwardzane światłem powłoki ochronne pochłaniają światło w zakresie UVA i światła widzialnego niebieskiego, a na rynku dostępnych jest wiele systemów utwardzania do utwardzania powłok lakierniczych. Najpopularniejsze konfiguracje do utwardzania to automatyczne przenośniki i stacjonarne systemy zalewania. Systemy punktowe są dostępne, ale są zalecane tylko do poprawek i małych obszarów utwardzania.Rys. 7. Płytka w systemie taśmowym
Ponownie ważne jest, aby wszystkie części systemu, w tym cały sprzęt i sama powłoka, były ze sobą kompatybilne. Intensywność, mierzona w miliwatach na centymetr kwadratowy (mW / cm2), to ilość energii, która dociera do powierzchni powłoki przy danej długości fali. Ilość całkowitej energii, która dotarła do powierzchni w określonym czasie, jest znana jako dawka, mierzona w milidżulach na centymetr kwadratowy (mJ / cm2). Krótko mówiąc, lampy o większej intensywności utwardzają powłoki szybciej, przy wszystkich innych zmiennych utrzymywanych na stałym poziomie, ale zbyt duża intensywność może spowodować uszkodzenie materiałów i części.Rys. 8. System punktowy - do napraw i małych obszarów
Ważne jest, aby zastosować optymalną intensywność aplikacji. Podobnie jak w przypadku innych materiałów światło-utwardzalnych, krytyczne znaczenie ma użycie radiometru w celu zapewnienia, że źródło światła będzie emitować z wystarczającą intensywnością, aby zapewnić całkowite i niezawodne utwardzenie powłoki.
Podsumowanie
Biorąc pod uwagę wartość komponentów elektronicznych w nowoczesnych samochodach, ich względną kruchość i trudne środowisko, w jakim się znajdują, a także rosnącą potrzebę oszczędzania miejsca, powłoki ochronne są idealnym rozwiązaniem problemu zoptymalizowanej ochrony. Światło-utwardzalne lakiery mogą być stosowane w celu zaoszczędzenia czasu i miejsca oraz zwiększenia wydajności, jednocześnie skutecznie chroniąc PCB w przemyśle motoryzacyjnym. Obecnie firmy, które chcą zarówno obniżyć koszty, jak i poprawić swoją pozycję w zakresie zgodności z przepisami środowiskowymi, mają do wyboru różnorodne materiały w 100% bezrozpuszczalnikowe i utwardzane promieniami UV.
W przypadku dodatkowych pytań prosimy o kontakt z firmą MILAR, dystrybutorem lakierów światło-utwardzalnych firmy DYMAX, gdzie wykwalifikowani pracownicy odpowiedzą na wszystkie Państwa pytania.
Autor: Michał Zieliński
Produkt Menadżer w firmie MILAR
Zdjęcia udostępnione dzięki uprzejmości firmy Dymax
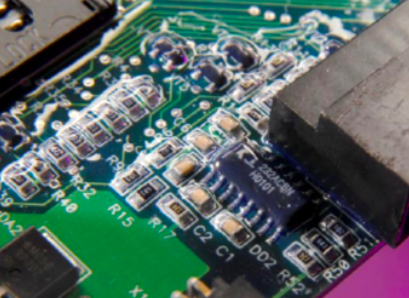
- Utwardzanie w cieniu - wtórne utwardzanie ciepłem i wilgocią w trudno dostępnych miejscach
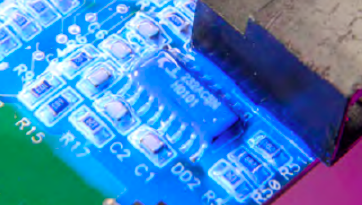
- Lakiery z technologią Ultra-Red® - technologia fluorescencyjna ułatwiająca kontrolę pokrycia
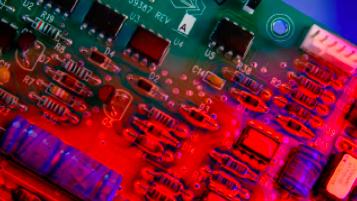
- Czarne lakiery – do ochrony poufnych informacji
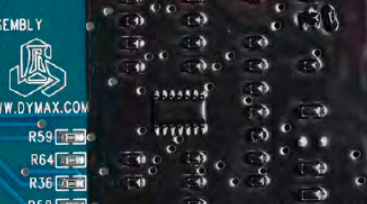
- Lakier ochronny o bardzo niskiej lepkości
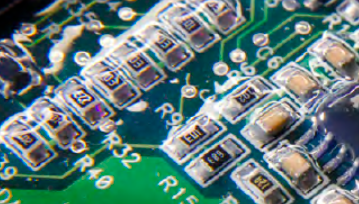
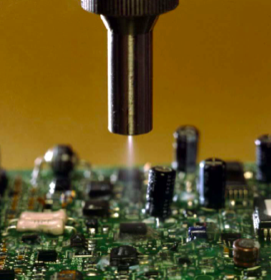
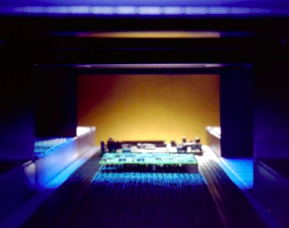
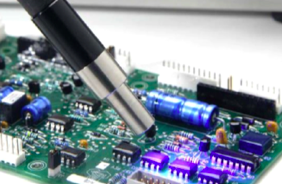
Zdjęcia udostępnione dzięki uprzejmości firmy Dymax