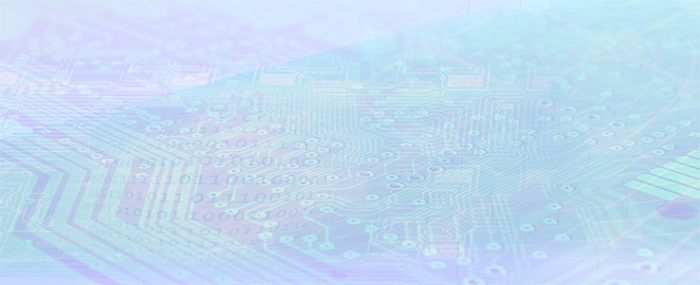
© Pixabay
Technologie |
Projektowanie PCB - zasady i rozmieszczenie modułów - cz. 1
Jak prawidłowo projektować płytki PCB w sposób oszczędny pod względem produkcji i układu? Jakie są najważniejsze zasady projektowania płytek PCB?
Obwody drukowane PCB są nieodłącznym elementem wszystkich urządzeń elektronicznych. Ich podstawową funkcją jest zapewnienie połączenia przewodzącego pomiędzy wtykami poszczególnych komponentów. Obwody drukowane PCB pojawiły się w późnych latach 60. ubiegłego wieku. Wtedy też opracowano zasady ich projektowania i produkcji, tworząc normy IPC. W dziedzinie obwodów drukowanych obwiązuje właśnie norma IPC-2221 "Ogólne standardy dotyczące płytek PCB".
Od czego zaczyna się projektowanie płytek PCB?
W elektronice stosuje się 3 typy komponentów i odpowiednie do nich metody lutowania:
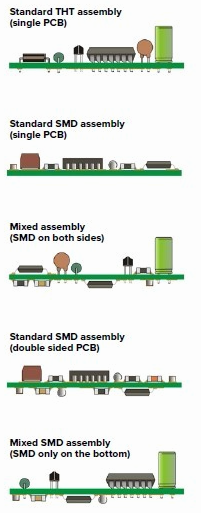
- podzespoły z końcówkami do montażu przewlekanego "Through Hole" – TH (osiowo, promieniowo) do lutowania ręcznego lub na fali,
- podzespoły z końcówkami do montażu powierzchniowego – "Surface Mount Devices" – urządzenia SMD, które można poddawać lutowaniu rozpływowemu w piecu lub na fali,
- podzespoły bez końcówek do montażu powierzchniowego – "Surface Mount Devices" – urządzenia SMD urządzenia do montażu powierzchniowego, które można poddawać lutowaniu rozpływowemu w piecu.
- minimalna szerokość ścieżki - W,
- minimalna odległość między ścieżkami - I,
- minimalna średnica przelotek (Via) - D.
- umieszczanie podzespołów w kolejności od tych o najwyższej do najniższej szerokość pasma,
- wzajemna separacja fizyczna określonych bloków funkcjonalnych (analogowych, cyfrowych, wej/wyj., zasilania),
- minimalizowanie odległości, aby wyeliminować pętle prądowe.
- Zasada jednopunktowa – A
- Zasada jednopunktowa równoległa – B
- Zasada wielopunktowa – C
- Filtrujące (Bypassing) – służą jako filtr szerokopasmowy zasilania dla całego obwodu drukowanego lub jego części. Eliminują wpływ indukcyjności wyprowadzeń zasilacza. (C1, C2, C8; C1 i C8 ≈ od 10µF do 1000µF). Zawsze należy w miarę możliwości dobierać kondensator o największej pojemności
- Miejscowe (Decoupling) – służą jako miejscowe źródła energii dla podzespołów i zmniejszają prądy impulsowe, które w przeciwnym razie rozchodziłyby się po całym układzie drukowanym. Kondensatory te muszą posiadać doskonałe właściwości częstotliwościowe. Należy je umieszczać możliwe blisko wtyku danego podzespołu (C4, C5, C6, C7 ≈ od 100pF do 0,1µF)
- Blokujące (Bulk) – służą za źródło energii do jednoczesnego zasilania wielu odbiorów o charakterze pojemnościowym. Jednak w pobliżu mikroprocesora: pojemność C3 ≈ 10µF.
- Minimalizowanie prądów w układów elektronicznych – dobór odpowiednich podzespołów i obwodów względem impedancji wejściowej itp.
- Minimalizowanie widma częstotliwości - unikanie szybkich podzespołów, które są zbędne (ze zboczem narastającym lub opadającym). Unikanie zbędnych, szybkich podzespołów komunikacyjnych.
- Filtracja i ochrona zacisków wejściowych/wyjściowych – zabezpieczenie przed wyładowaniami elektrostatycznymi (ESD), wykorzystywanie efektu przejścia, ograniczanie promieniowania z wyprowadzeń.
- Minimalizowanie pętli prądowych i długości ścieżek – minimalizowanie pętli prądowych przez stosowanie zasad prawidłowego rozmieszczenia podzespołów, ścieżek, prowadzenia masy, ścieżek zasilających, prawidłowe stosowanie kondensatorów filtrujących.
- Ekranowanie – jednoczesne tłumienie promieniowania i poprawa odporności na zakłócenia.
- Jak zapewnić możliwość przeprowadzenia badania obwodów drukowanych?
- Jak wygląda technologia produkcji obwodów drukowanych?