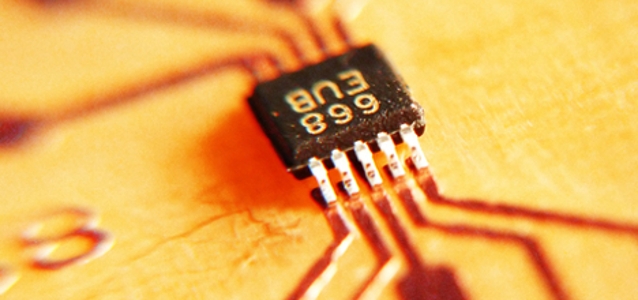
© kornwa dreamstime.com
Technologie |
Rysunek 1: Ułożenie jednostronne
Montaż dwustronny.
Realizacja jest wolniejsza, a elementy są narażone na powtórne rozgrzewanie w piecu.
Rysunek 2: Ułożenie dwustronne
Montaż dwustronny występuje w układach o dużym stopniu „upakowania”. Najczęściej są to urządzenia małe, gdzie powierzchnia obwodu musi być jak najmniejsza.
W tym przypadku należy pamiętać, że jedna strona płytki będzie narażona na powtórny przejazd przez piec. Na tej stronie należy więc umieścić elementy bierne, które są mniej wrażliwe na wysokie temperatury. Na tej stronie nie umieszczamy jednak elementów o dużych gabarytach i znacznej masie, np. dławików SMD, ponieważ istnieje ryzyko, że takie elementy mogą oddzielić się od obwodu, ze względu na możliwość ponownego upłynnienia lutu.
Przy lutowaniu rozpływowym, niezależnie od tego czy montaż będzie jedno lub dwustronny ważne jest odpowiednie doprowadzenie ścieżek do elementów. Ważne jest aby spoiwo lutownicze rozgrzewało się i stygło równomiernie na wszystkich padach komponentu.
Rysunek 3. Zalecane (prawa strona) i niezalecane (lewa strona) sposoby doprowadzania ścieżek do elementów.
Ogólne uwagi co do prowadzenia ścieżek:
• Układ i powierzchnia ścieżek powinien być zrównoważony, tak aby zachować podobne powierzchnie warstwy miedzi po obu stronach druku, w celu zapewnienia równomiernego nagrzewania podczas lutowania i minimalizować tym samym odkształcenia płytek, powodowane różną rozszeżalnością cieplną warstw.
• Ograniczać do minimum długości ścieżek.
• W miarę możliwości i wymagań ścieżki powinny być jak najszersze, ale połączenie ścieżki z polem lutowniczym nie powinno przekraczać 1/3 szerokości pola lutowniczego. W przypadku podłączenia do dużej powierzchni miedzi należy stosować odsunięcie powierzchni miedzi od padu i połączenie z padem za pomocą kilku cienkich ścieżek. Ta metoda pozwala na równomierne nagrzewanie i stygnięcie lutowia i konsekwencji zapobiega podnoszeniu się (efekt nagrobkowy) elementów podczas procesu lutowania rozpływowego.
• W przypadku układów scalonych do pola lutowniczego powinna być dołączona jedna ścieżka, nie należy wykonywać połączeń wyprowadzeń dużymi powierzchniami jak i nie powinno się bezpośrednio łączyć wyprowadzeń.
• Zachowywać odpowiednią odległośc ścieżek od krawędzi płyki, zwyczajowo nie mniej niż 0,3 mm.
• Wszystkie ściezki powinny mieć kąt rozwarty, kąt prosty powinien powstawać z połączenia kątów rozwartych.
• Maska lutownicza jak i opisowa nie może nachodzić na pola lutownicze.
• Co do grubości ścieżek i odstępów międzi nimi należy zapoznać się z możliwościami wykonania PCB.
• Nie należy w miarę możliwości stosować granicznych wielkości norm i wymagań technologicznych, nawet przy płytkach z bardzo gęstym upakowaniem. Tam gdzie jest to możliwe nadal należy stosować zasadę grubszych ścieżek i większych odstępów.
Artykuł opublikowano dzięki uprzejmości firmy Kompania Elektroniczna. Autor: © Wojciech Mućka
Projektowanie obwodów drukowanych dla elementów SMD
Nie ma jednego przepisu na dobry obwód drukowany. Każdy projekt jest inny dlatego ważne jest indywidualne podejście do każdego problemu projektowania.
Projektujesz elektronikę? Zarezerwuj 4 października 2018 roku na największą w Polsce konferencję dedykowaną projektantom, Evertiq Expo Kraków 2018. Przeszło 50 producentów i dystrybutorów komponentów do Twojej dyspozycji, ciekawe wykłady i świetna, twórcza atmosfera. Jesteś zaproszony, wstęp wolny: kliknij po szczegóły.Projektant często ma zadanie zaprojektować płytkę PCB dla istniejącego schematu ideowego, zaprojektowanego przez inną osobę. W takiej sytuacji z góry ma zarzucone zastosowane elementy i nie ma dużej swobody w doborze obudów elementów i zastosowanej techniki montażu. W przypadku gdy projektant jest twórcą całości urządzenia, ta swoboda daje luksus panowania nad projektem od początku do końca. Można wybrać sobie technologię już na etapie koncepcji. Projektując należy poczynić założenia i wybrać najkorzystniejszy wariant wdrożenia do produkcji. Układy elektroniczne przeznaczone do produkcji średnio i wielkoskalowej w bardzo dużym stopniu składają się z elementów SMD, które będą montowane automatycznie, co za tym idzie lutowanie będzie odbywać się w rozpływowo w piecu lutowniczym. Tu najważniejszą kwestią jest znajomość możliwości technologicznych wykonawcy. Często projektant musi wybrać wykonawcę swojego urządzenia i poznać jego możliwości. Oczywiście nie można pominąć kwestii ekonomicznych, ale też nie można zbytnio upraszczać konstrukcji. W dużych firmach wyposażonych w odpowiedni park maszynowy, projektant zna te możliwości i może zaprojektować układ w oparciu o znaną mu technologię. Jako że nie ma jednego sprawdzonego przepisu na obwód drukowany, należy stosować kilka dobrych praktyk w tym procesie. Montaż jednostronny. Jest najszybszy w realizacji, a elementy nie są narażone na powtórne rozgrzewanie w piecu.© Evertiq


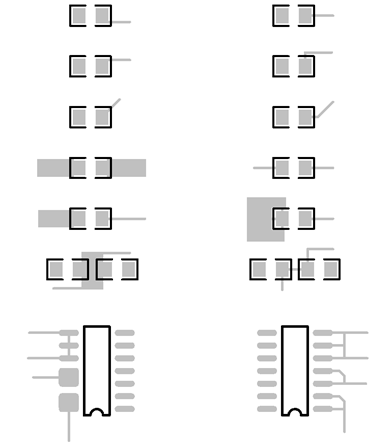